Food Manufacturing: Pain Points for Productivity, Safety, & Efficiency
29/09/2022

When the average person tucks into their favourite meal or takes a sip of their favourite drink, they may not instantly think about how their product has been produced or packaged.
Unless they’re a big fan of Inside the Factory, of course – you know, the one presented by MasterChef veteran, Greg Wallace.
And in that case, we salute their curiosity for wanting to know how everything from cheese to chicken kievs is getting from production floor to plate.
For food and drink manufacturers, the production floor is the bread and butter of the operation. But it’s not always plain sailing when it comes to worker productivity, safety, and efficiency.
As a trusted adviser to a range of food manufacturers across the UK, we’ve put together a list of some of the most common pain points they face on a daily basis.
Productivity
PAIN POINT – Having an ineffective workflow system
An effective workflow system is paramount for production floor managers. It is a vital ingredient when it comes to creating a thriving environment.
But it’s not easy thing to get right. Especially when the conveyer belt of food and drink products has to keep moving – with minimal disruption.
SOLUTION – Use job ticketing software to streamline and automate workflow tasks
To remove any headaches of workers not carrying out tasks at the right time, or recording them properly, you need to implement a workflow system that will streamline and automate tasks.
With Job Ticketing, tasks can be created, assigned and tracked via a centralised system or radio network. Real-time updates will be sent to staff member’s radio device, and they can keep on top of when to start and finish a task.
Once they accept a job and complete it, the data will be captured and ready for analysis.
PAIN POINT – Minimising machine downtime
Machine downtime is one of the biggest bug bears food and beverage manufacturers face. In fact, research in the past has suggested that machine downtime costs the industry £180 billion a year.
That’s an expensive headache to overcome, and one that requires a solution in place that can’t be bought over the counter.
SOLUTION – Use Extended Alarm Management
To minimise the impact of machine downtime, you should use Extended Alarm Management – which is an alarm systems where critical machinery can be synced to a two-way radio.
Once the machine and the radio are synced together, radio users can receive alerts that there’s a problem.
PAIN POINT – Noisy environment making it hard to hear each other
You may be familiar with the song, Food, Glorious Food, but the tune that plays to that classic isn’t quite the same as the one that belts out on the production floor.
Heavy machinery, a conveyer belt of products, and the sound of people working combine to create a noisy environment.
SOLUTION – Use radios with the Intelligent Audio feature
To combat background noise, businesses can take advantage of radio devices that have an Intelligent Audio feature. Put simply, Intelligent Audio will automatically increase or decrease the volume of the radio, depending on the background.
PAIN POINT – Ensuring staff are in the right place
People are the powerhouse behind any good operation. Without them, the supply chain – that relies on readily available products – suffers.
But managing them effectively and knowing they’re in the right place at the right time, is never straightforward.
SOLUTION – Use indoor and outdoor location positioning
There is something that can make it less of a burden, though. And that ‘thing’ is indoor and outdoor location positioning. With the use of GPS and Bluetooth beacons, you can ensure your team are always where they should be.
Safety
PAIN POINT – Protecting lone workers during their shift
Lone working is super common in the UK. And the theme continues in food manufacturing. Working in isolated environments comes with a higher risk of accident and injury, especially when surrounded by heavy machinery and potentially explosive equipment.
SOLUTION – Use Lone Worker
To help keep your lone workers as safe as possible, you can use the Lone Worker feature on a range of digital two-way radios. This feature will send regular alerts to a user’s radio and will be tracked when the lone worker presses a button to confirm that they are okay.
This is a great way to ensure the welfare and safety of lone workers is being checked on a regular basis.
PAIN POINT – Reporting incidents and accidents accurately
Incident and accidents can’t always be avoided in a busy working environment. But if you’re not 100 percent sure what happened, then you can’t move forward and reduce the amount of incidents that take place.
SOLUTION – Voice recording and audit reports
You can monitor and report incidents more accurately with Voice Recording. This is a feature where radio-to-radio conversation are recorded.
You then use the recording to playback the conversation via an MP3 file. This will then allow your health and safety function to run training initiatives based on real-life incidents on site.
PAIN POINT – Reacting to worker injuries quickly
With so much going at once, it can be easy take your eye off the ball. Especially in respect to staff whereabouts.
If something serious happens, you need to make sure you have the right data intelligence to react quickly.
SOLUTION – Use Man Down
And react quickly you can. With a solution known as Man Down.
This is a feature that is built into digital two-way radios. In a nutshell it works out when a radio is at abnormal angle.
Once the radio is at an unusual angle, a prompt will be sent to the radio user. If the radio user is unresponsive, then it may well mean that something isn’t right – and you can react to it straight away.
PAIN POINT – Struggling with communication coverage
If your staff struggle to communicate, because you have signal problems across your operation, then it can put their safety in jeopardy.
SOLUTION – Choose the right seamless network infrastructure
We will help you overcome your coverage issues by creating a seamless network infrastructure that suits your surroundings and your needs.
Visit our infrastructure page to see all of the solutions we offer for your business.
Efficiency
PAIN POINT – Getting important updates out to staff
Sometimes your workforce needs to know what to do an instant, and not have to stop and take a phone call before carrying on with their day. But when mobile phones are accessible, what do they do?
SOLUTION – Use text messaging
Not everyone will know this, but digital two-way radios with screens and keypads give you the ability to send and receive text messages.
You can also send out pre-defined messages, where you can relay important site updates to a group of radio users at once. Very handy when you need split second thinking or everyone to know something at once.
PAIN POINT – Production workers and off-site workers communicating effectively
Every business in food manufacturing has connections to a supply chain that can stretch from one side of the world to the other.
But if communication between production floor staff and head office staff can’t be consistent, then neither can the success of the supply chain.
SOLUTION – Use Telephone Interconnect
When people think of two-way radios (or walkie talkies) they probably picture a scenario where a radio can only talk to another radio.
But over the years technology has advanced, and in this day and age radios can talk to mobile phones and landline devices. This is made possible by a piece of software known as Telephone Interconnect.
PAIN POINT – Our workers struggle to communicate and carry tasks out at the same time
Productivity is pivotal in the food and drink production business. But if workers find themselves in a situation where they’re having to stop working in order to pick up their radio, then productivity will suffer.
SOLUTION – Use VOX (Voice Activated Communications)
Many digital two-way radios have a feature known as VOX (Voice Activated Communications) where a user can simply use their voice to broadcast a message, without the need to touch a push-to-talk (PTT) button.
PAIN POINT – Getting the most out of our two-way communication system
Whenever you buy communication devices, the hope is that they will work straight out of the box, regardless of your building structure(s) and environment.
It’s never as straightforward as this, as there’s several layers of complexity to consider before deciding you can use devices or a system with no external help.
SOLUTION – Choose expert engineering services with Eemits
We’ve been advising and supporting businesses (for over 36 years) on the right communication solution for their needs.
This includes services such as over-the-air programming, preventive maintenance, and reactive maintenance. We leave no stone unturned when it comes to designing and implementing digital two-way radio systems.
News Archive
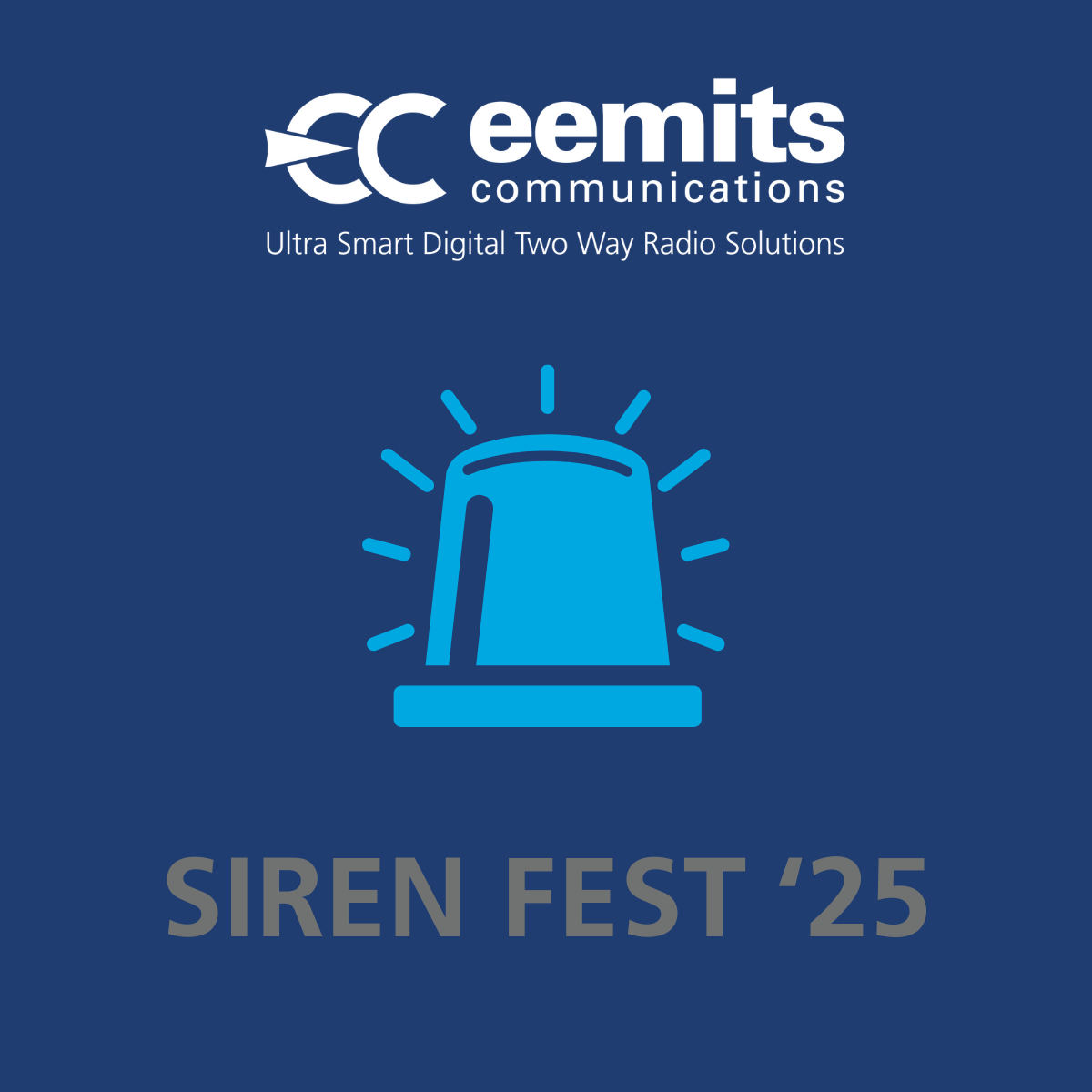
31/03/2025
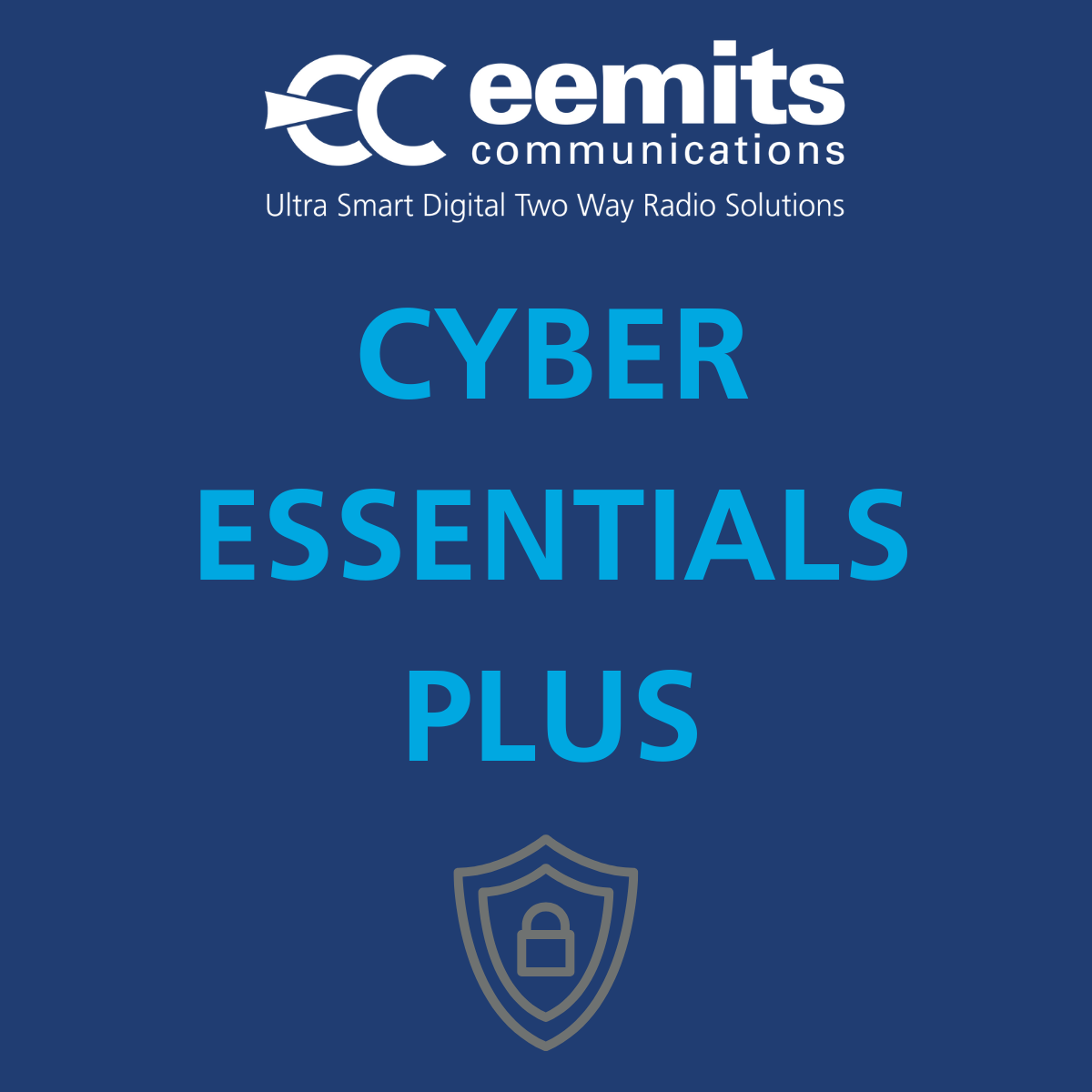
26/03/2025
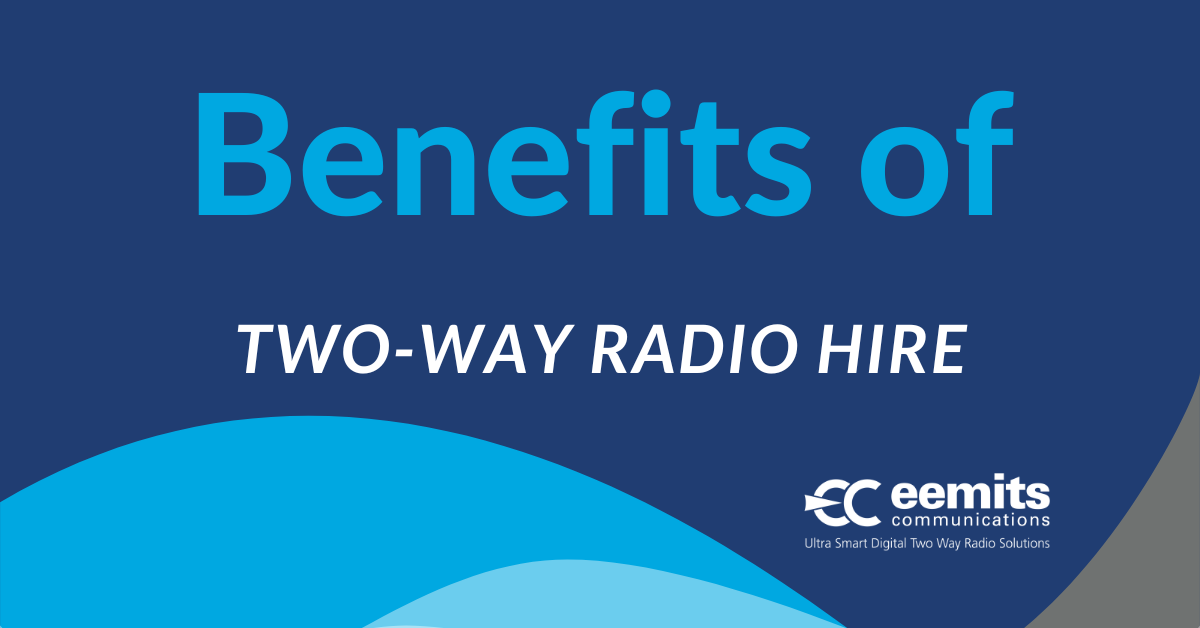
19/02/2025
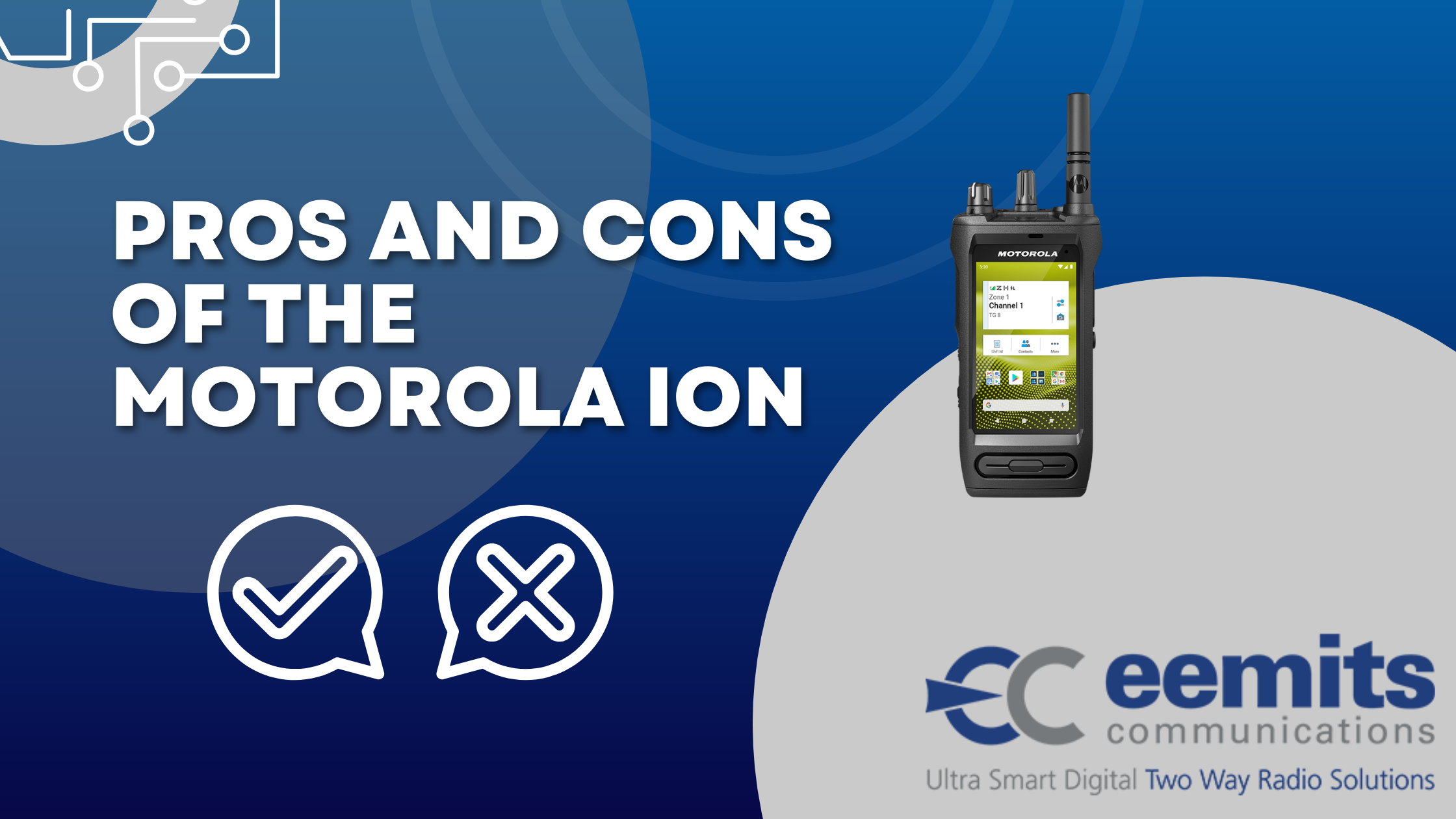
13/02/2025
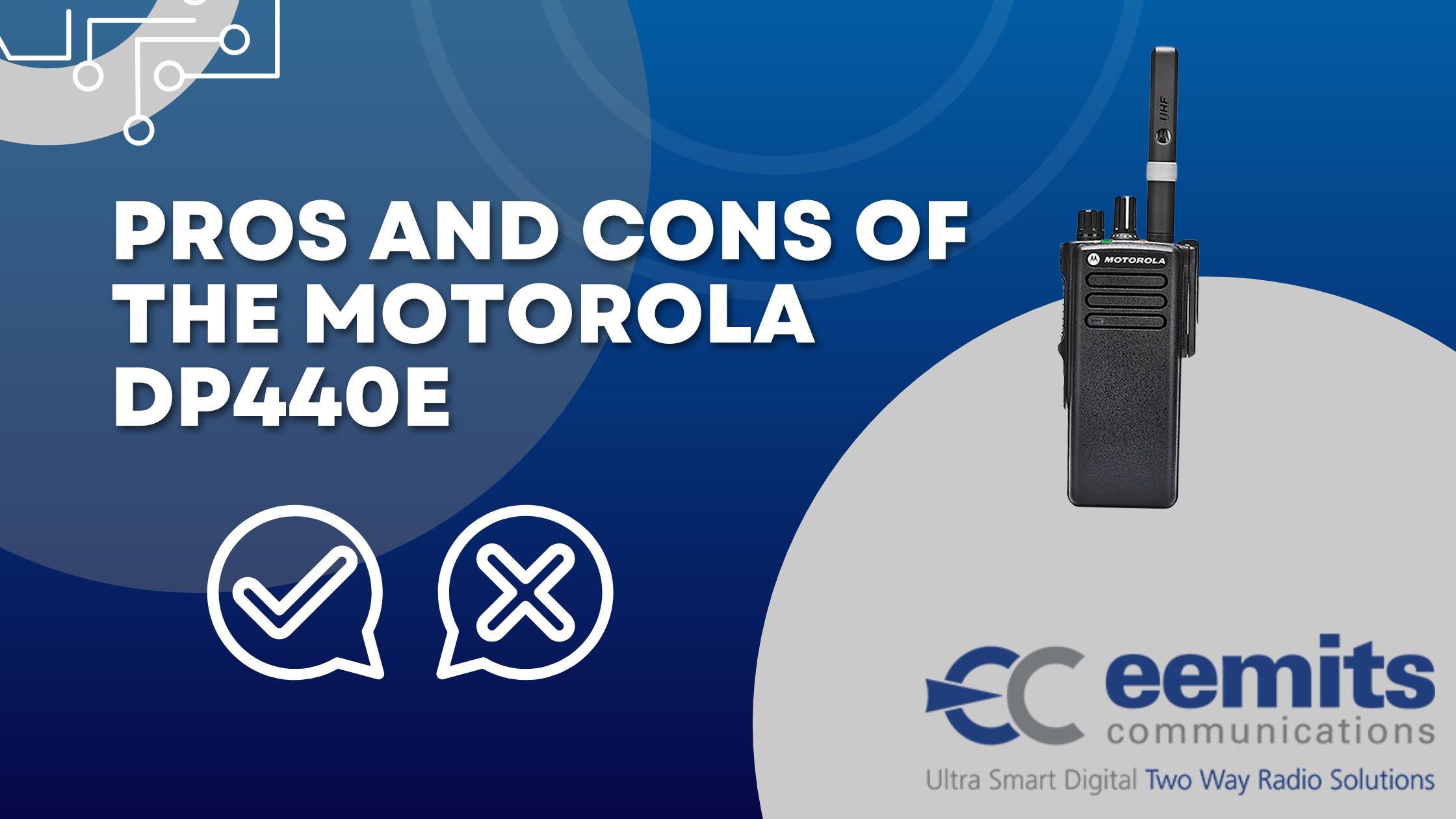
13/02/2025
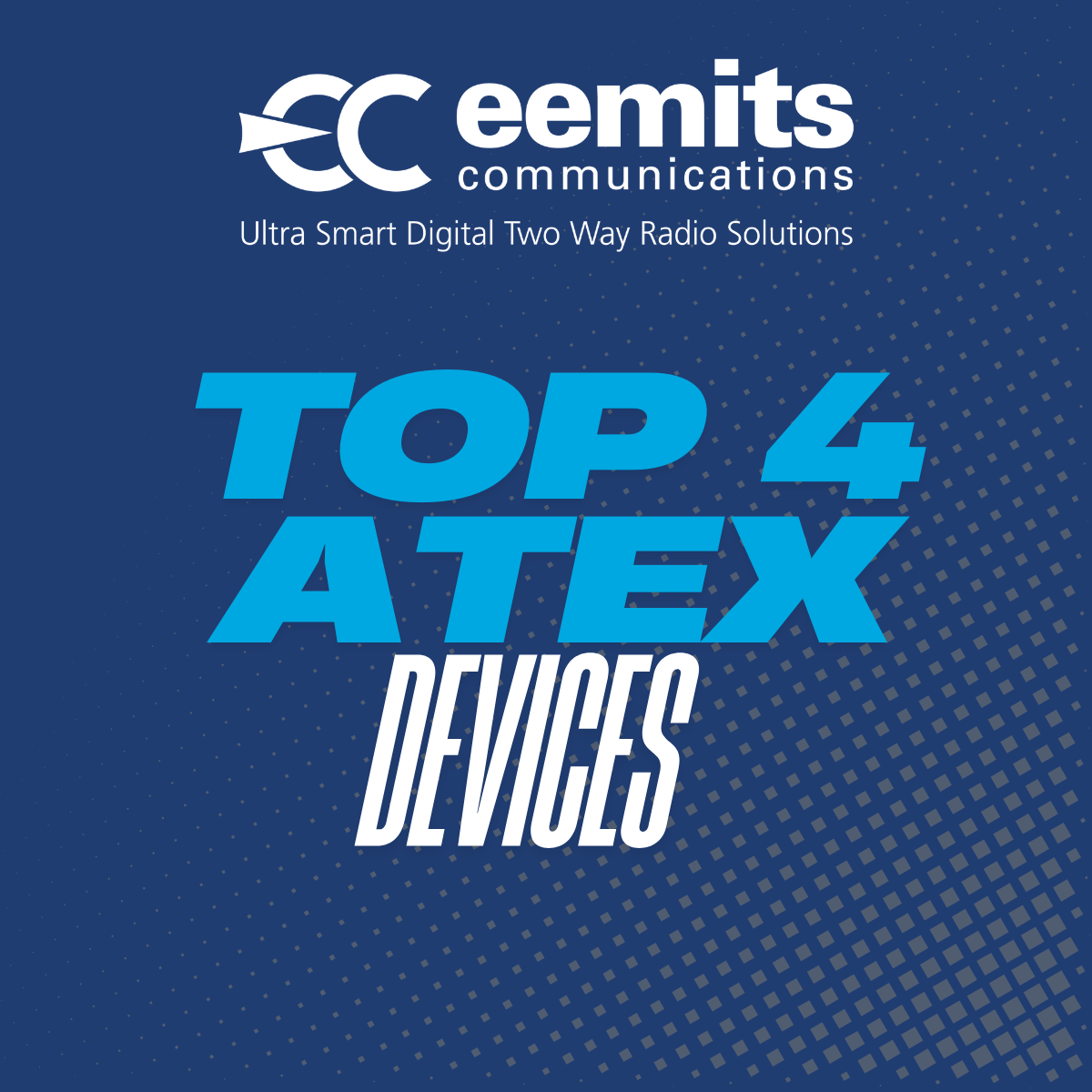
07/02/2025
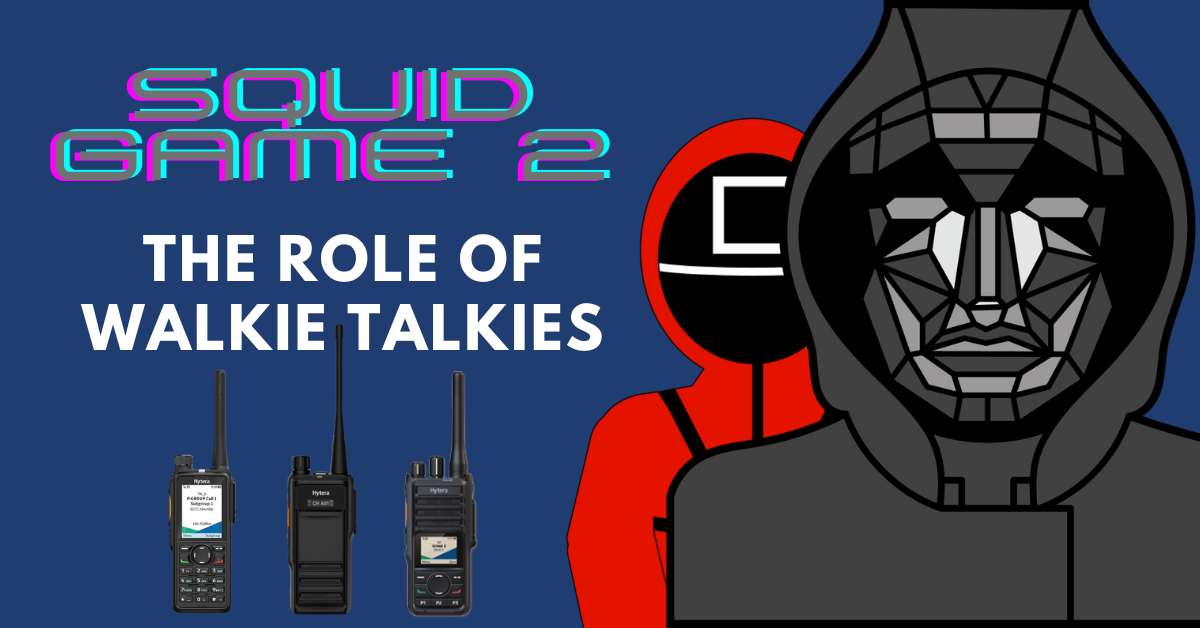
14/01/2025
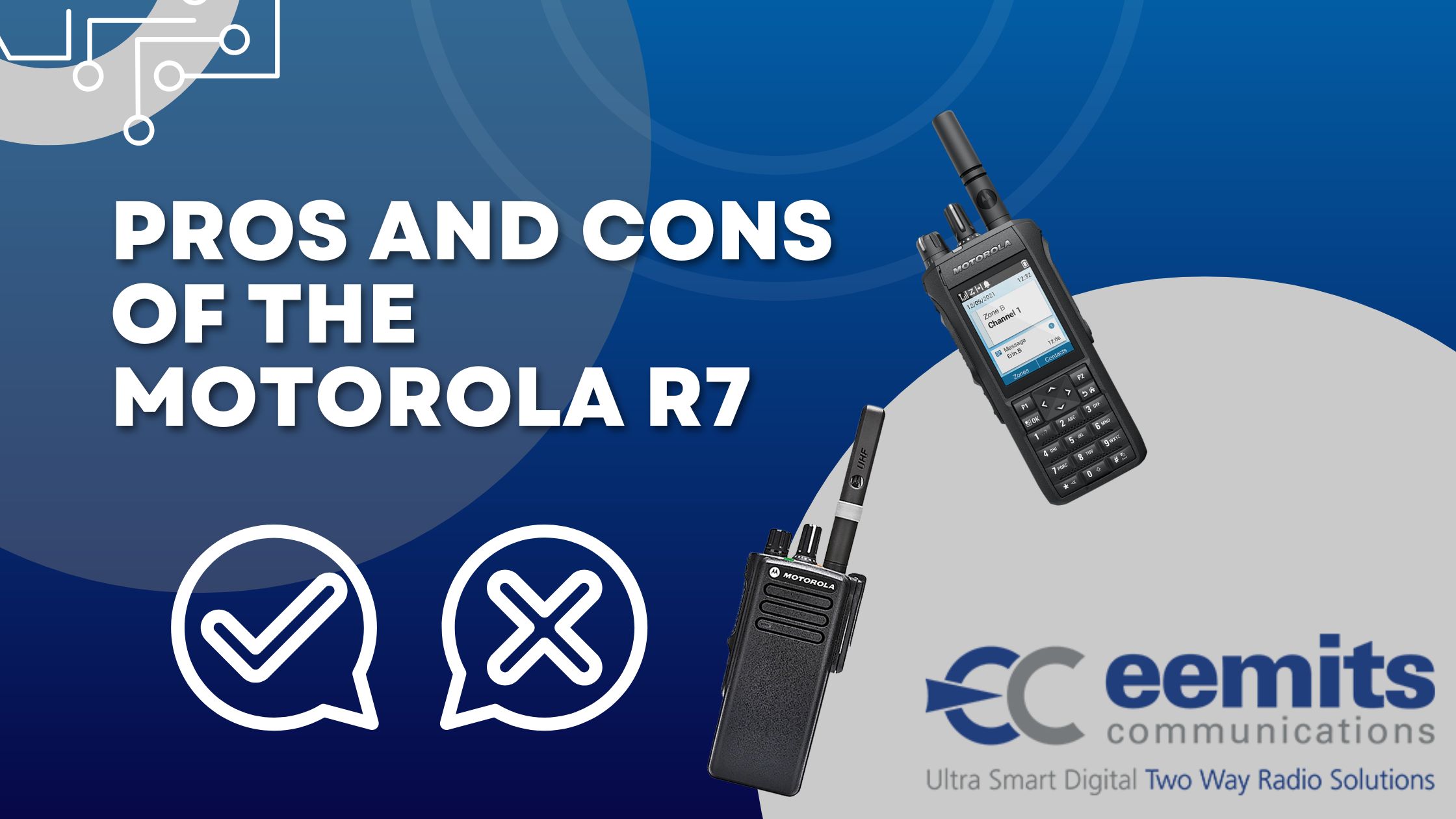
17/12/2024
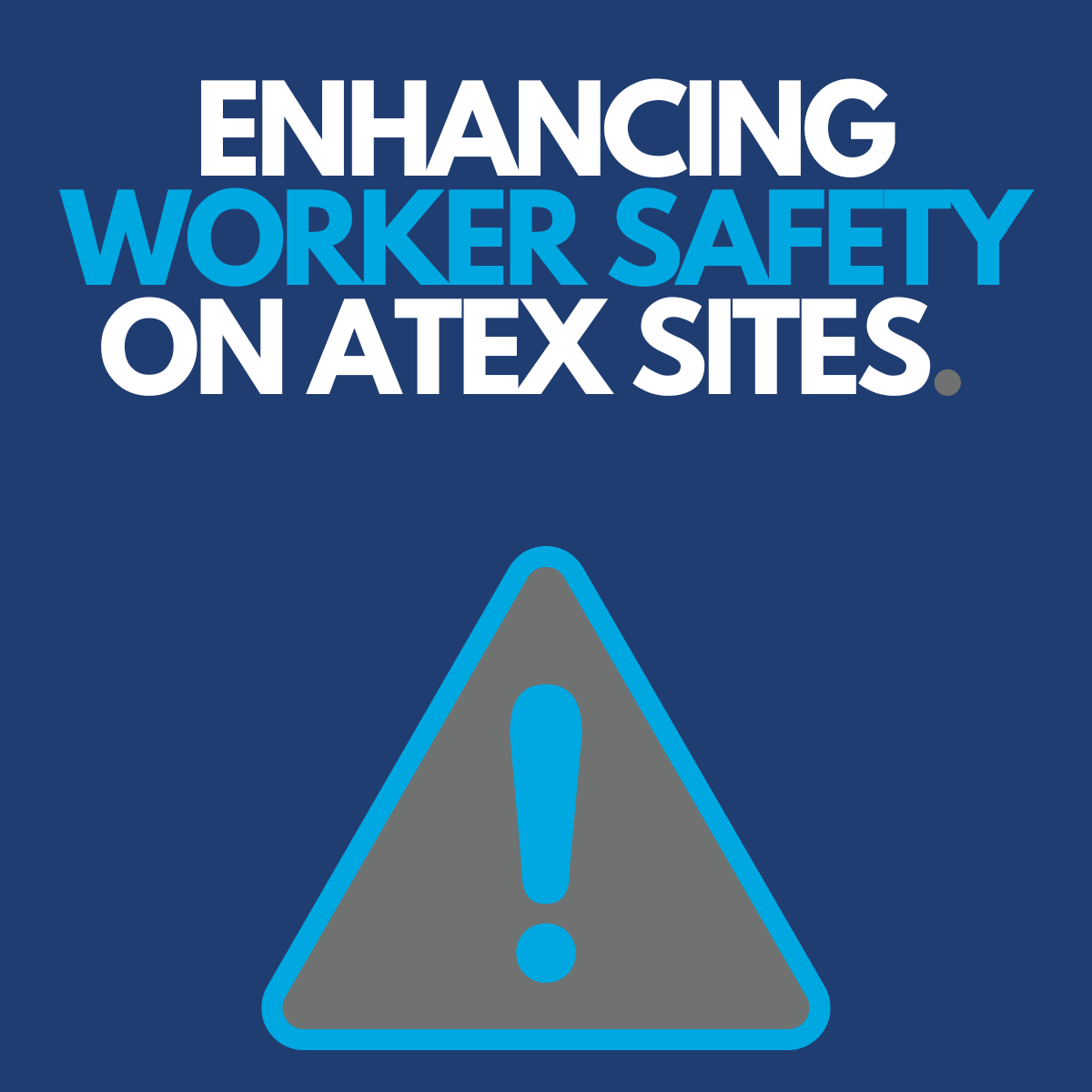
17/12/2024
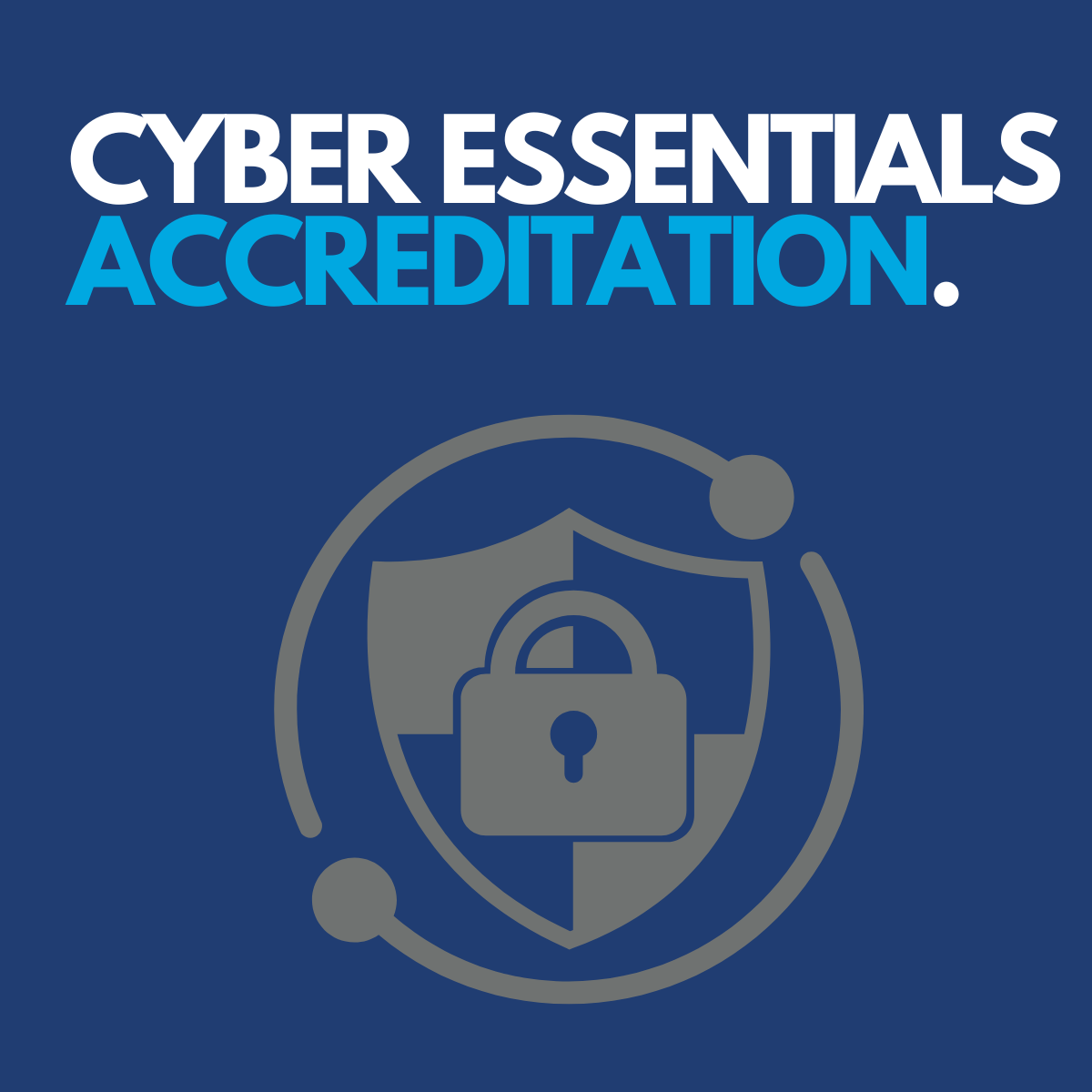
13/12/2024
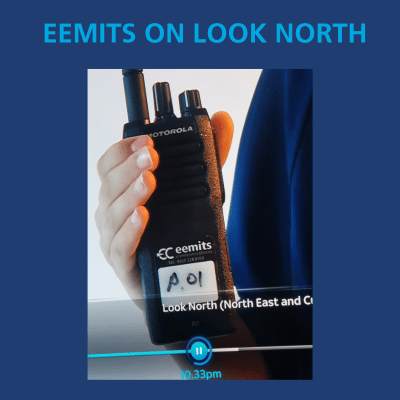
31/05/2024
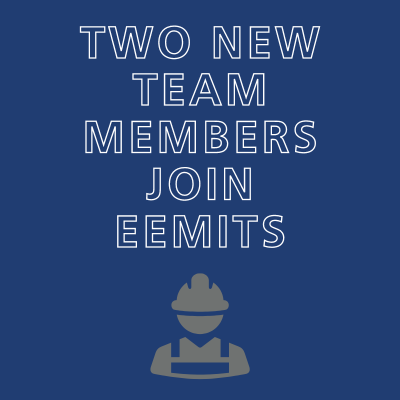
28/05/2024
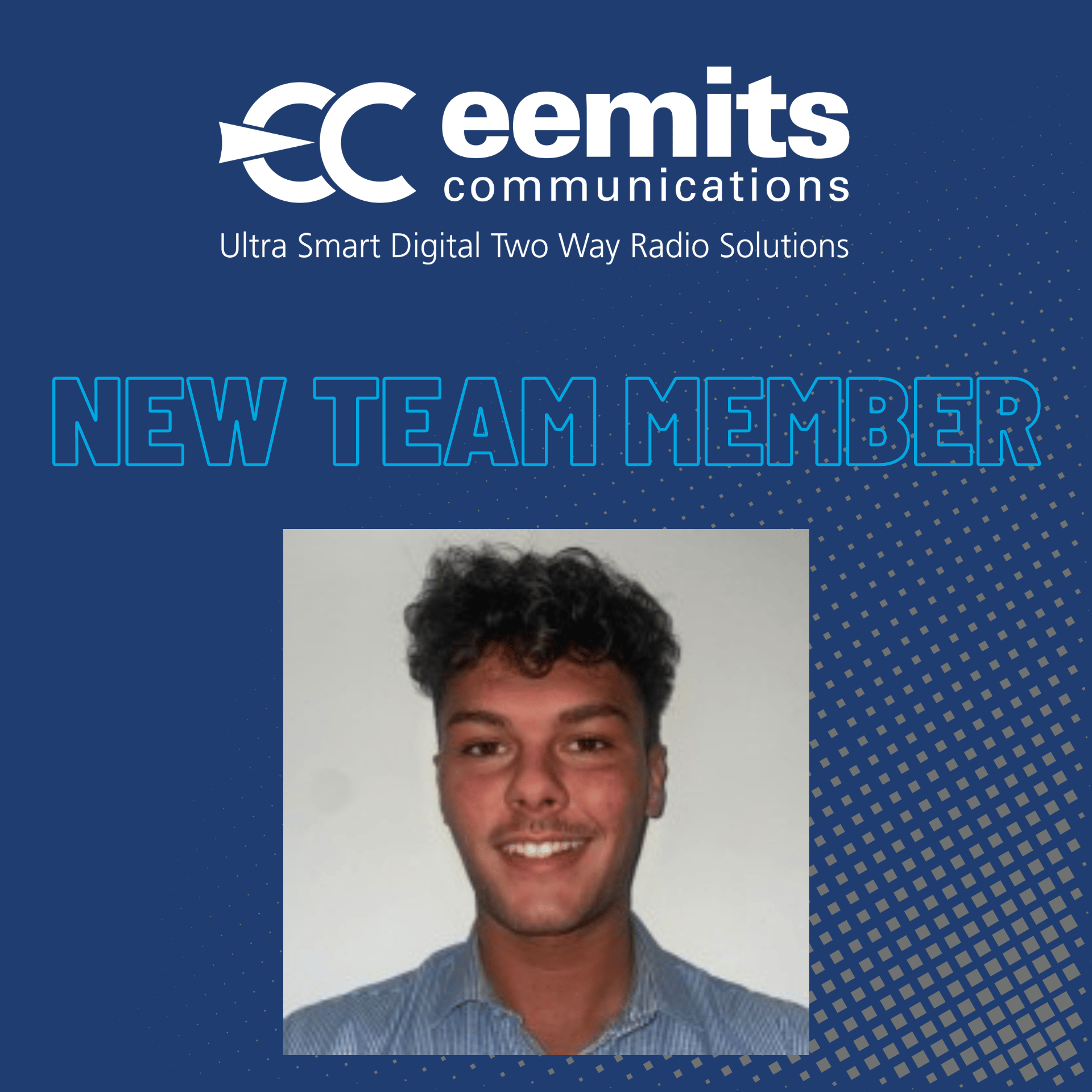
25/04/2024
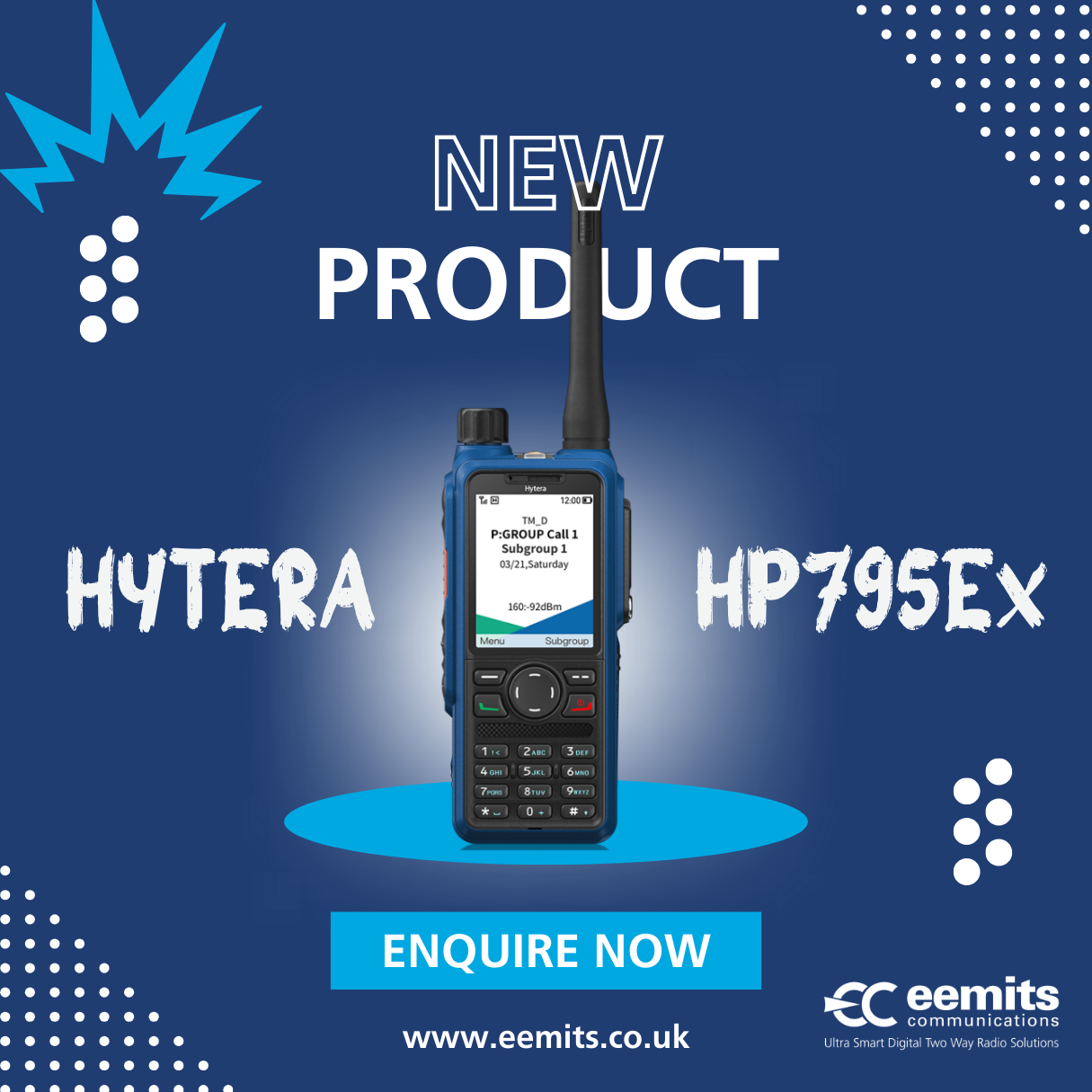
05/02/2024
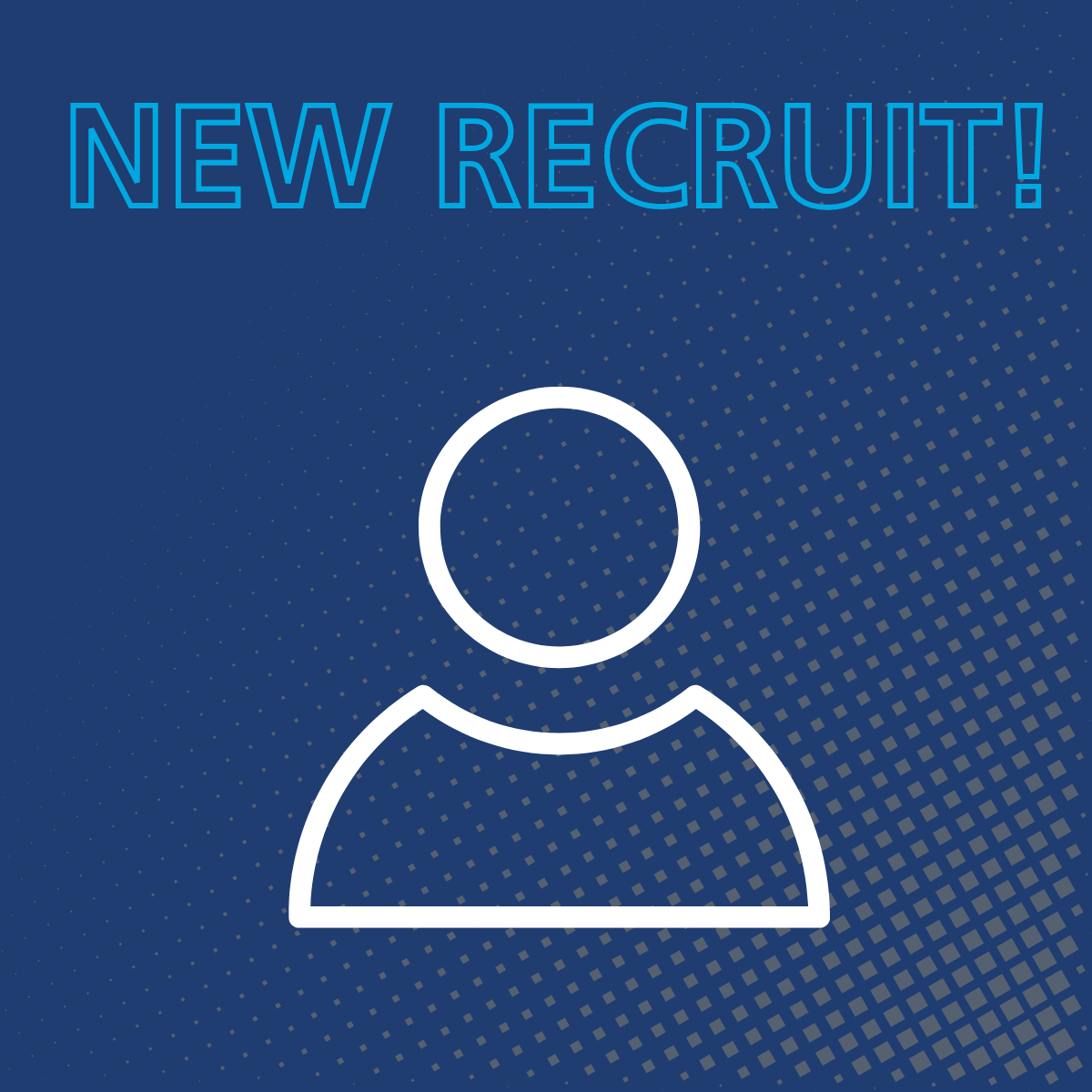
31/01/2024
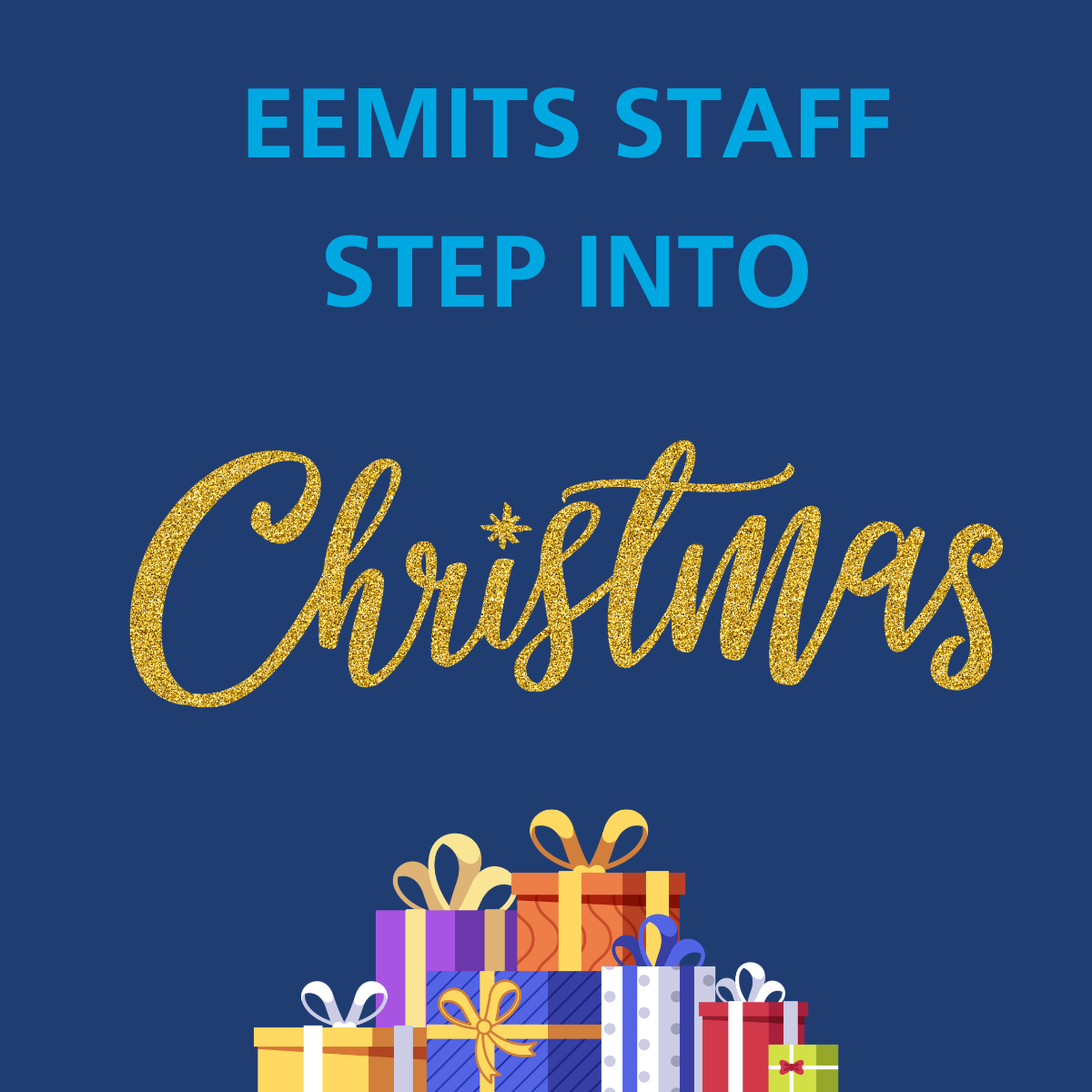
22/12/2023
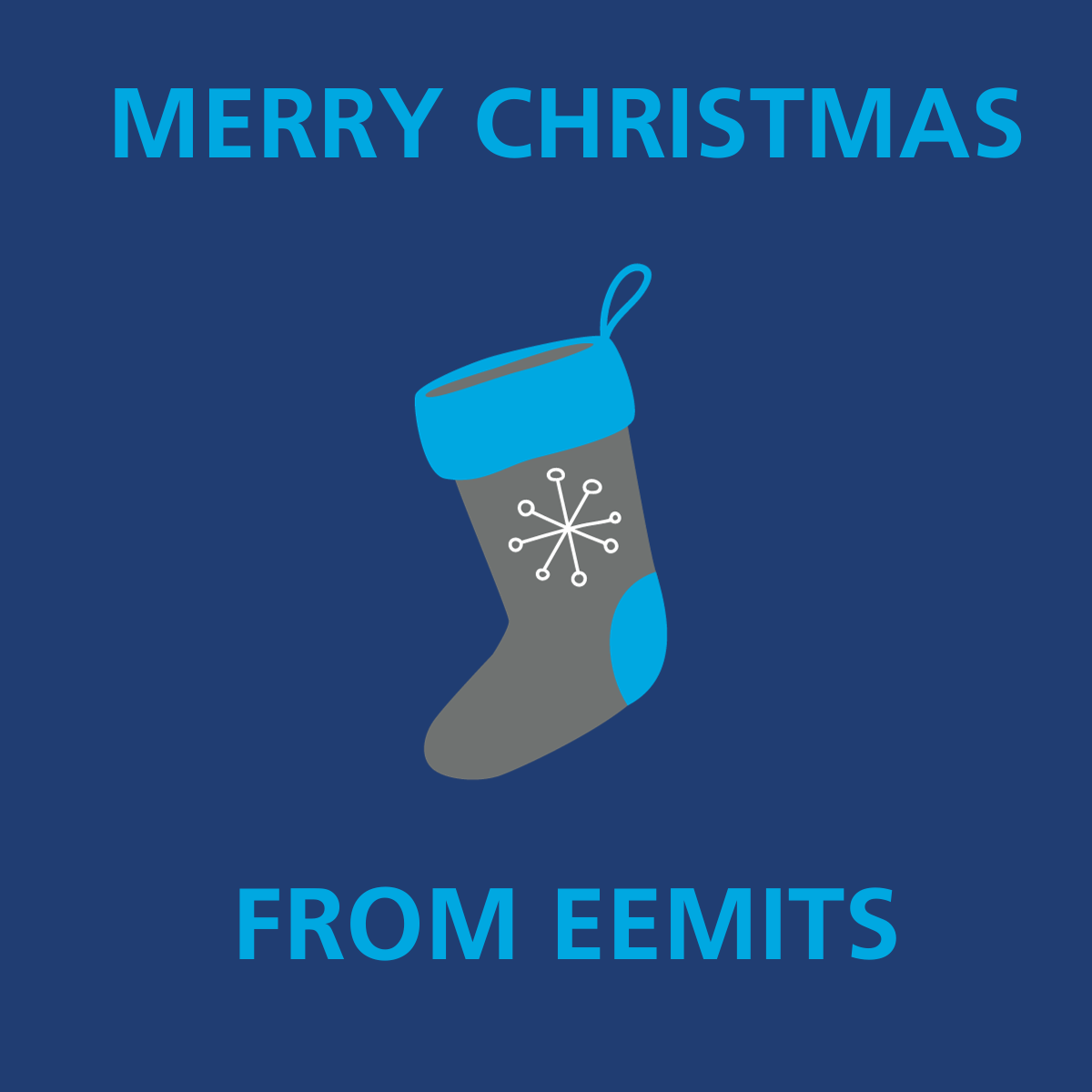
22/12/2023
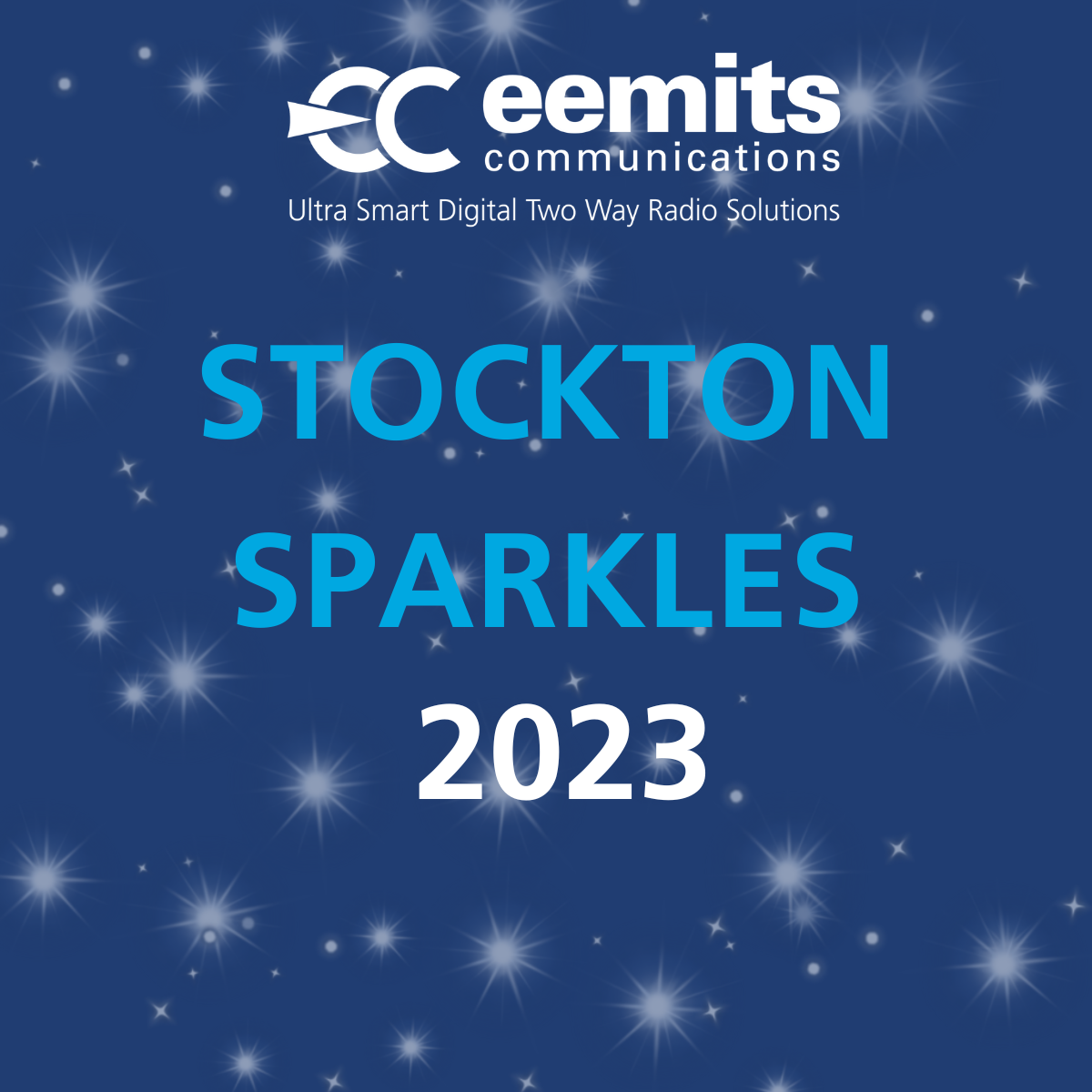
22/11/2023
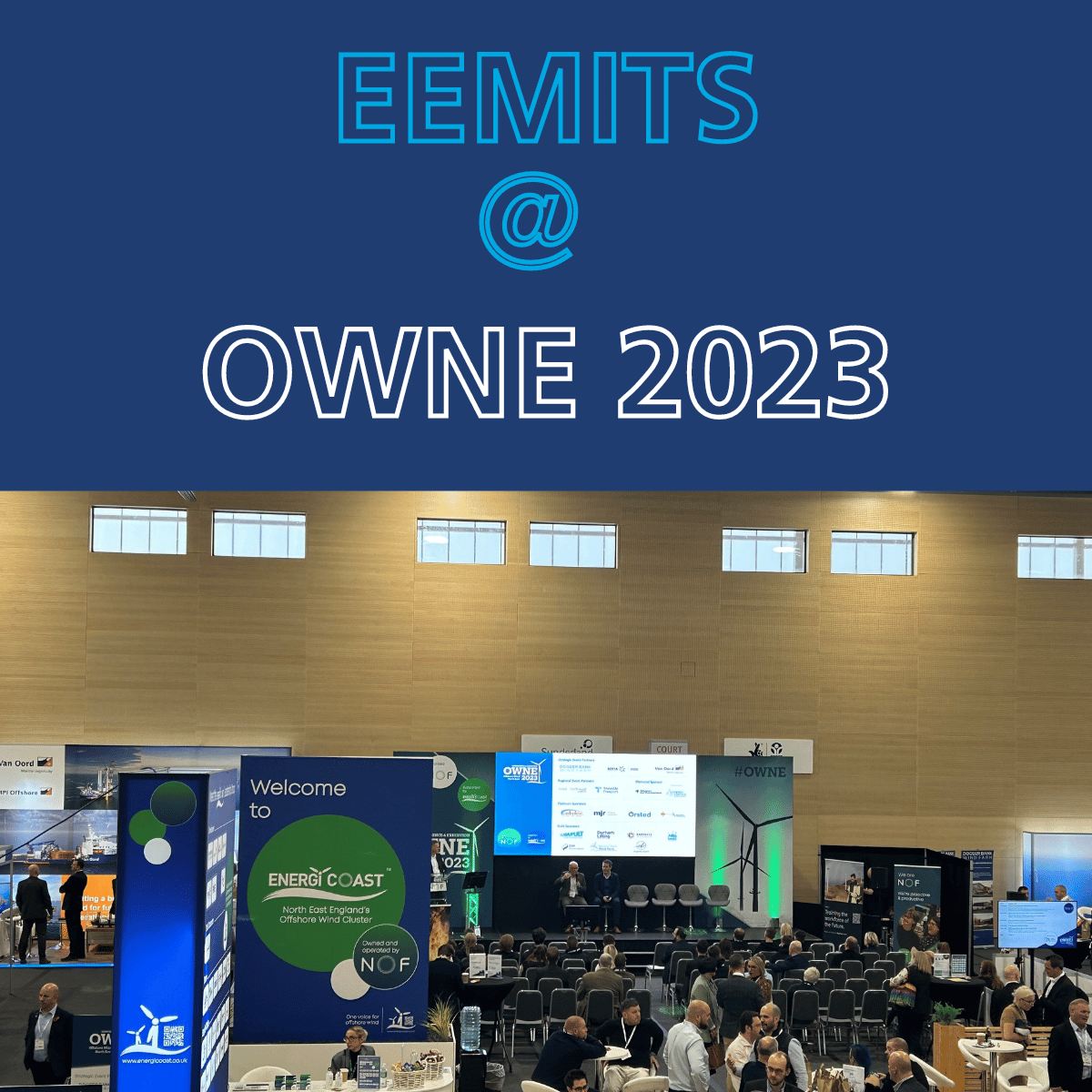
10/11/2023
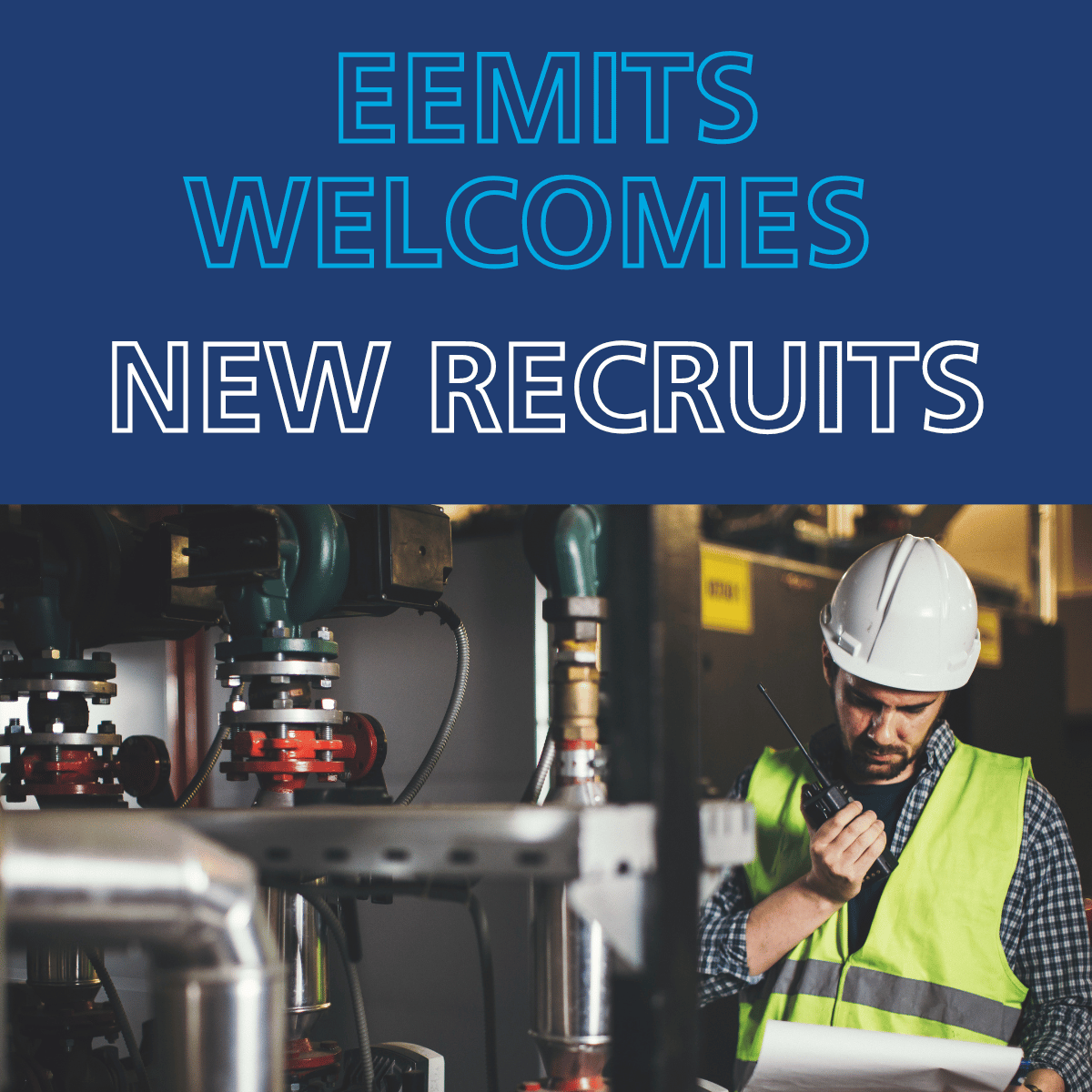
27/10/2023
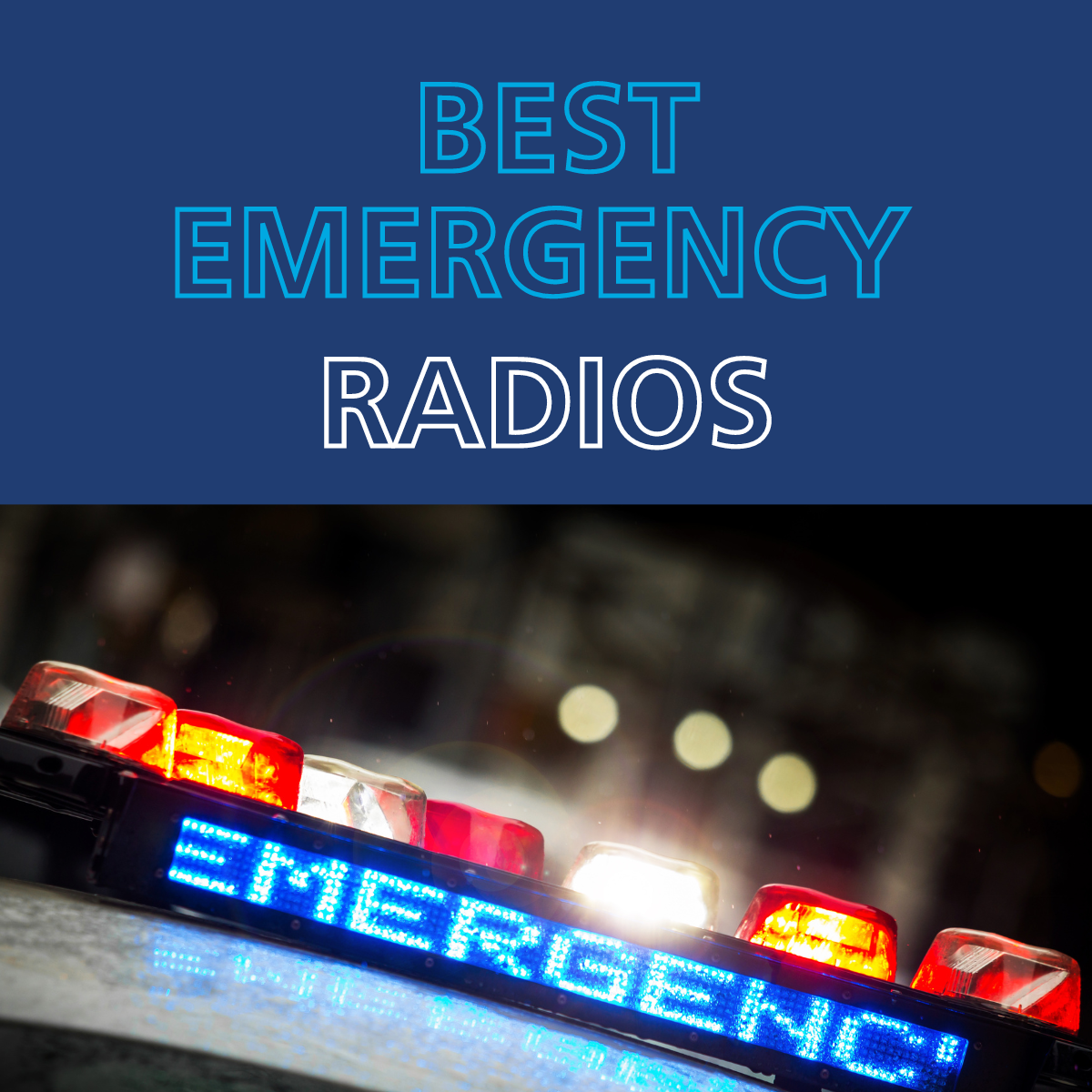
26/10/2023
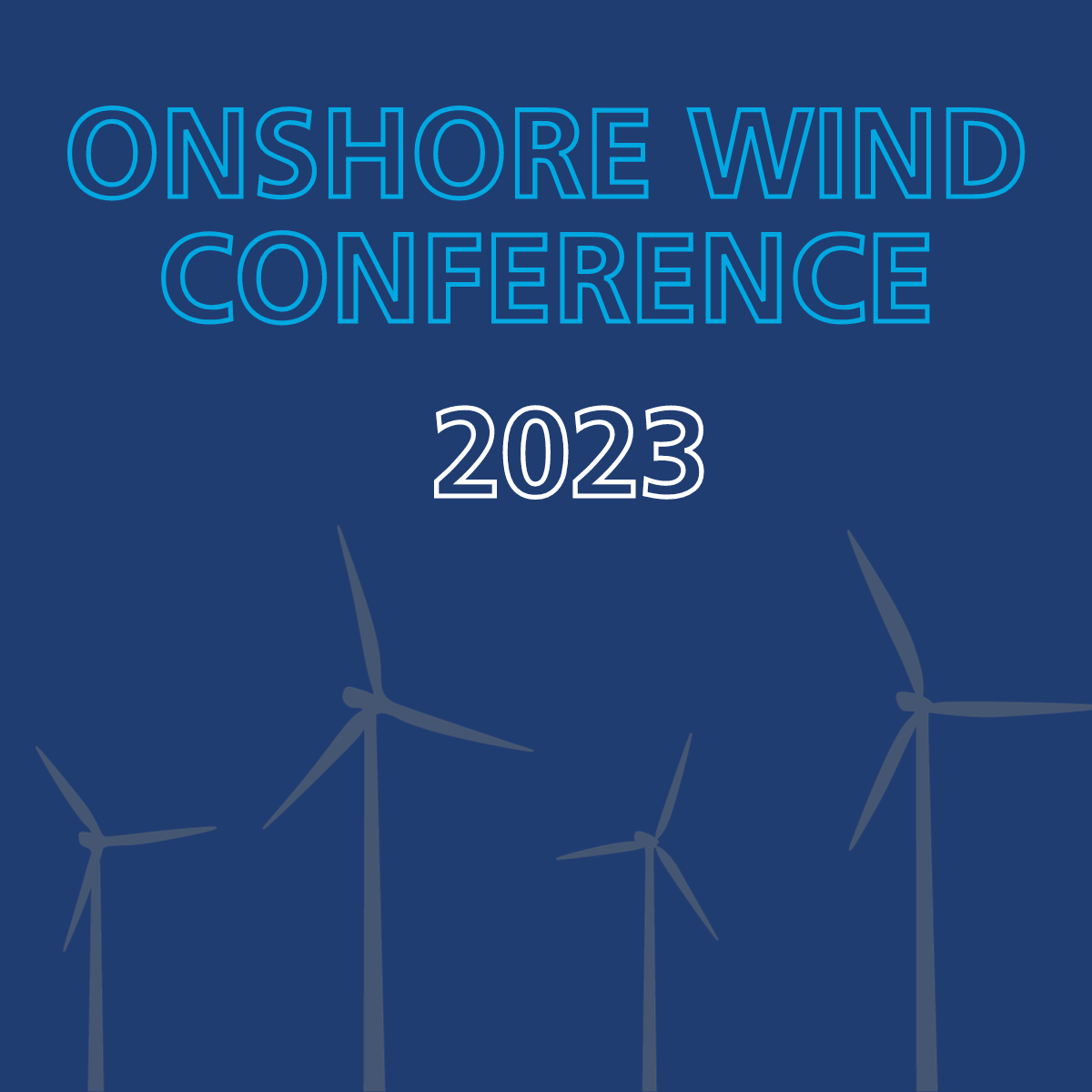
22/09/2023
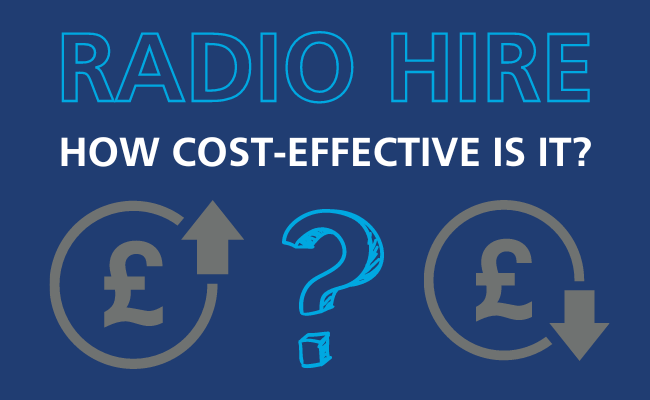
31/08/2023
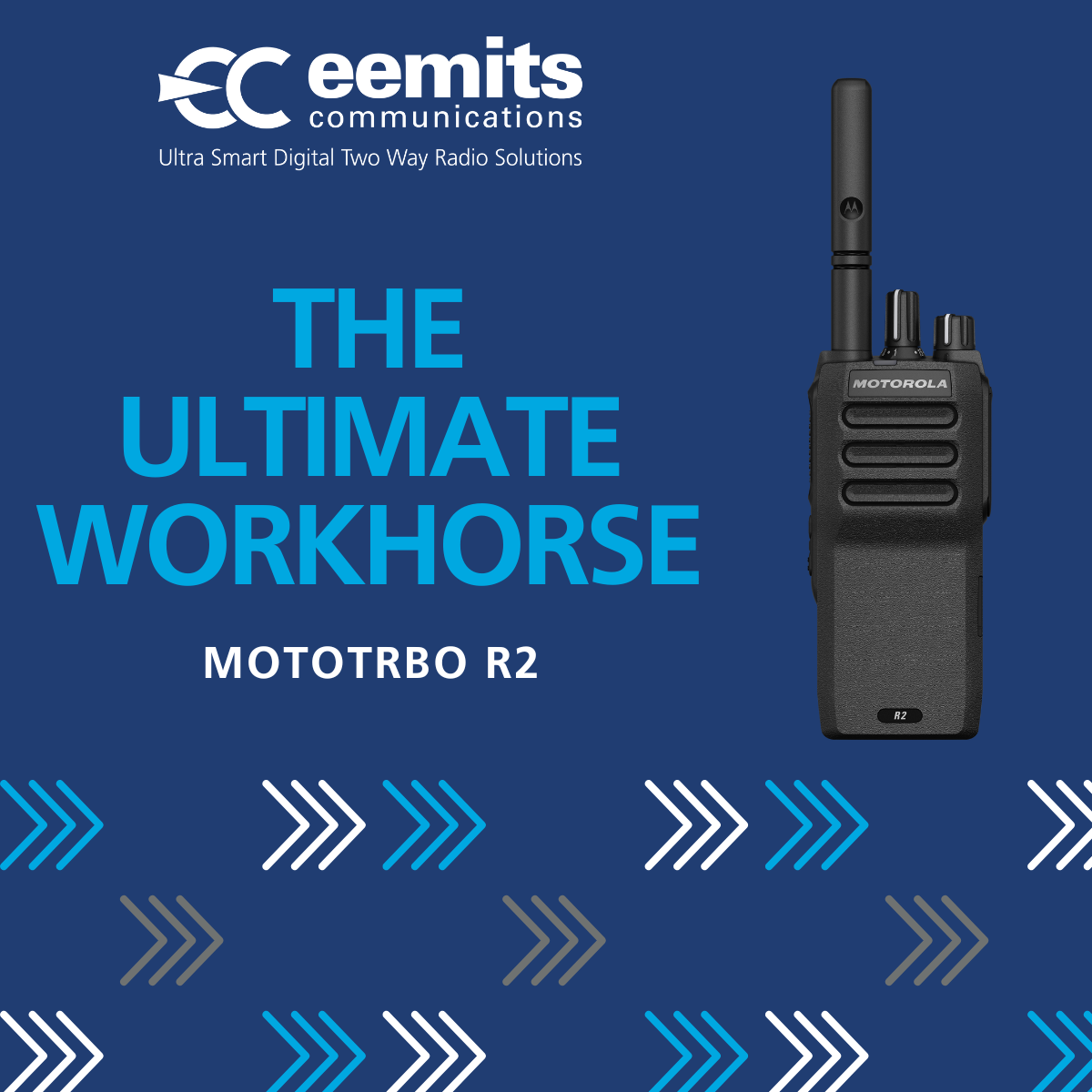
09/05/2023
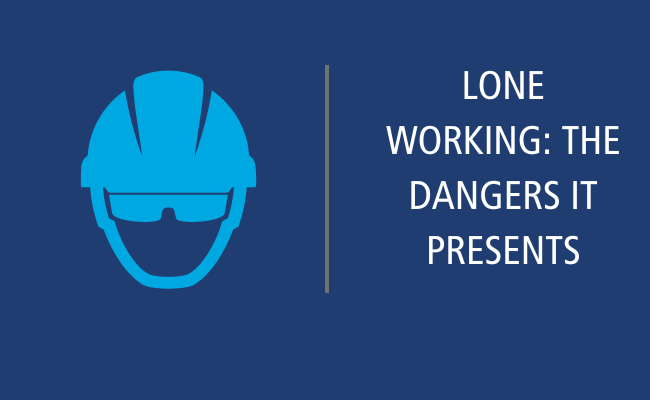
23/12/2022
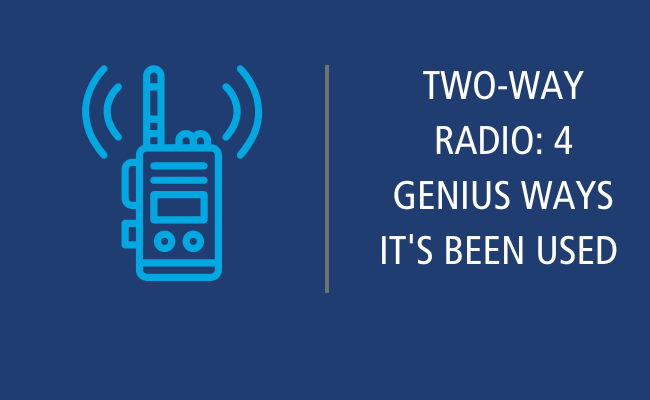
30/11/2022
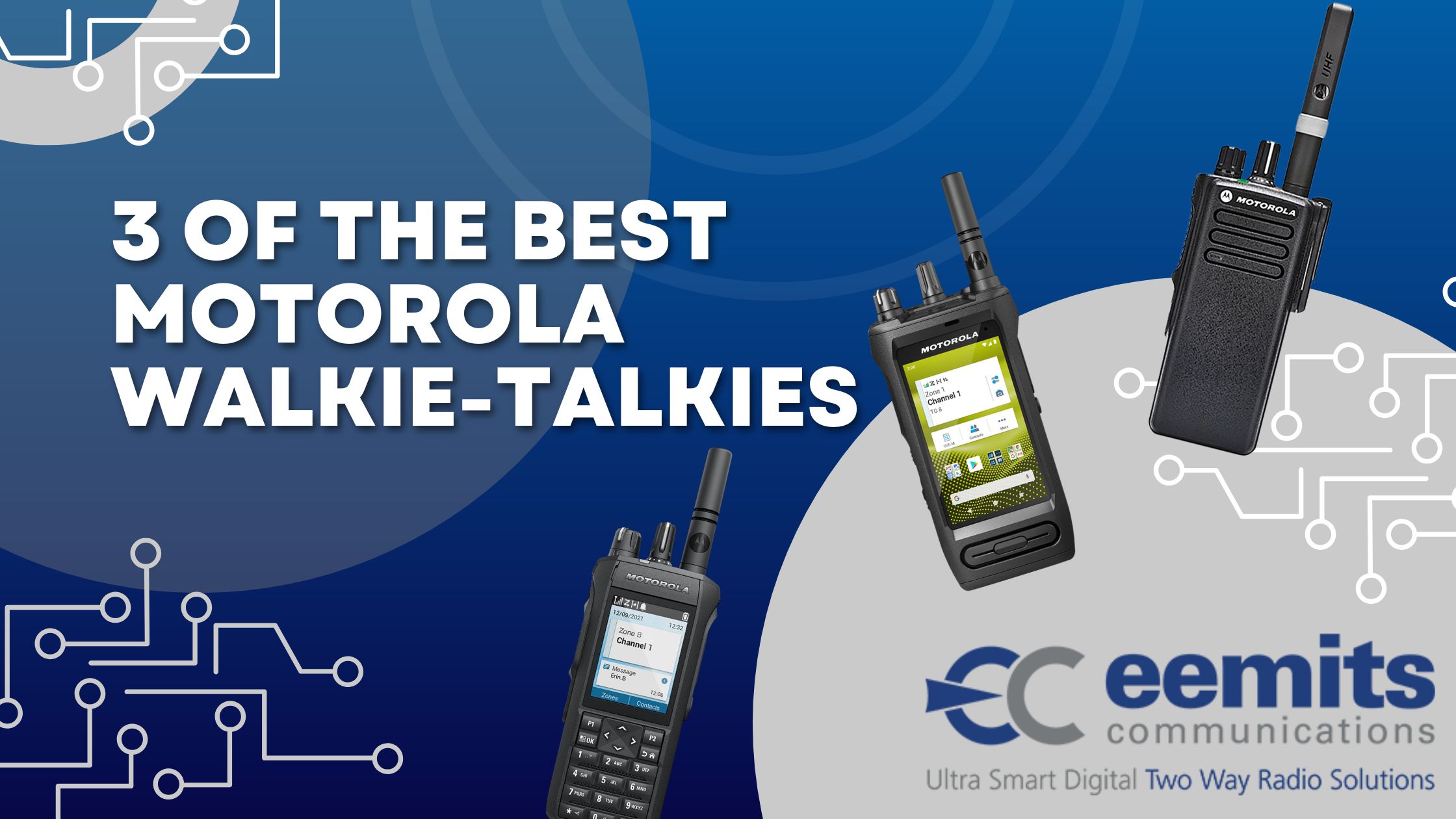
31/10/2022
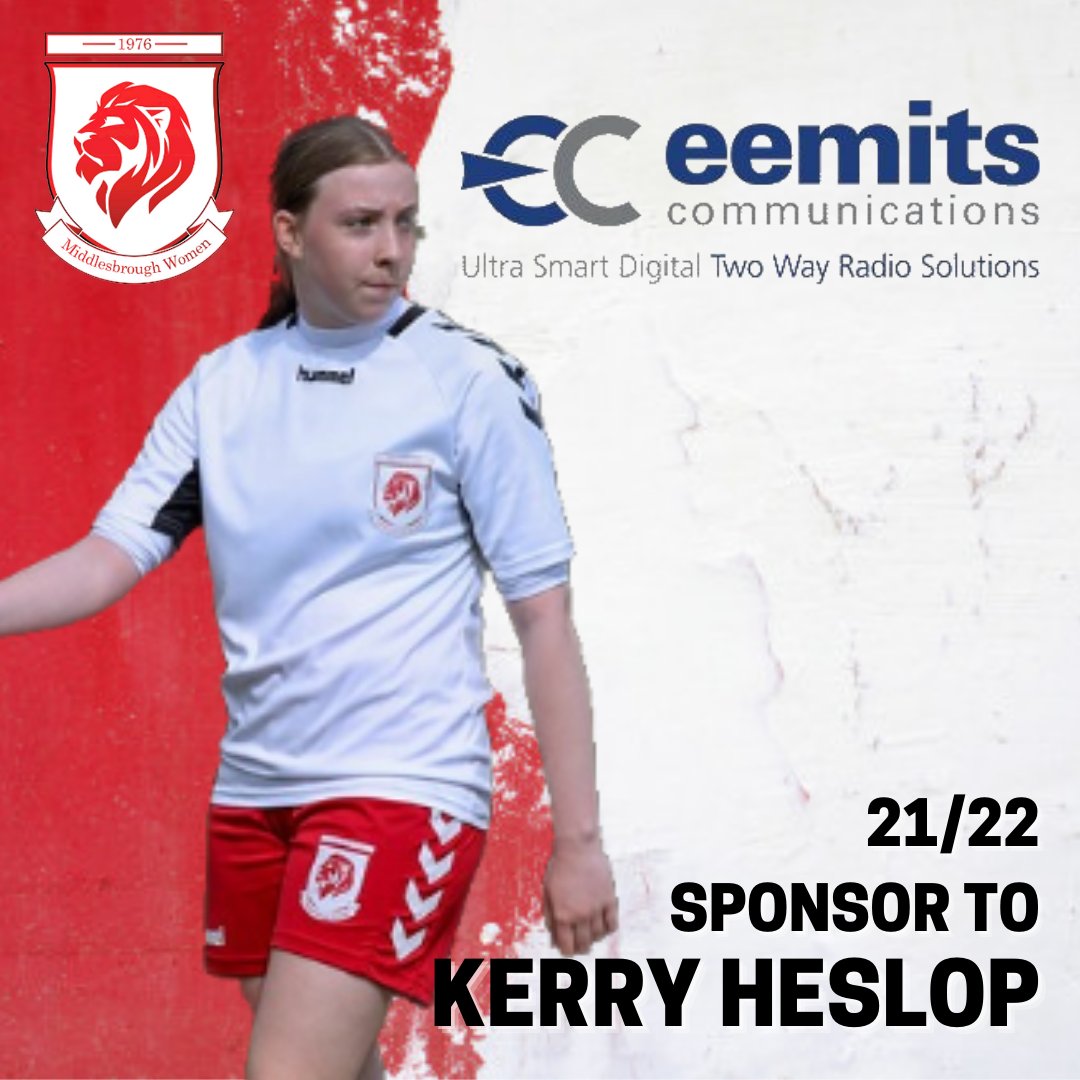
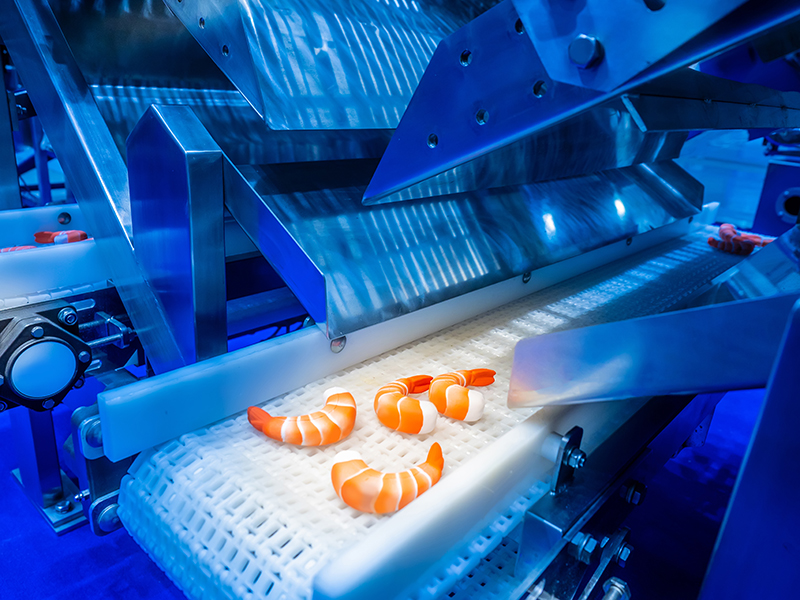
28/01/2021
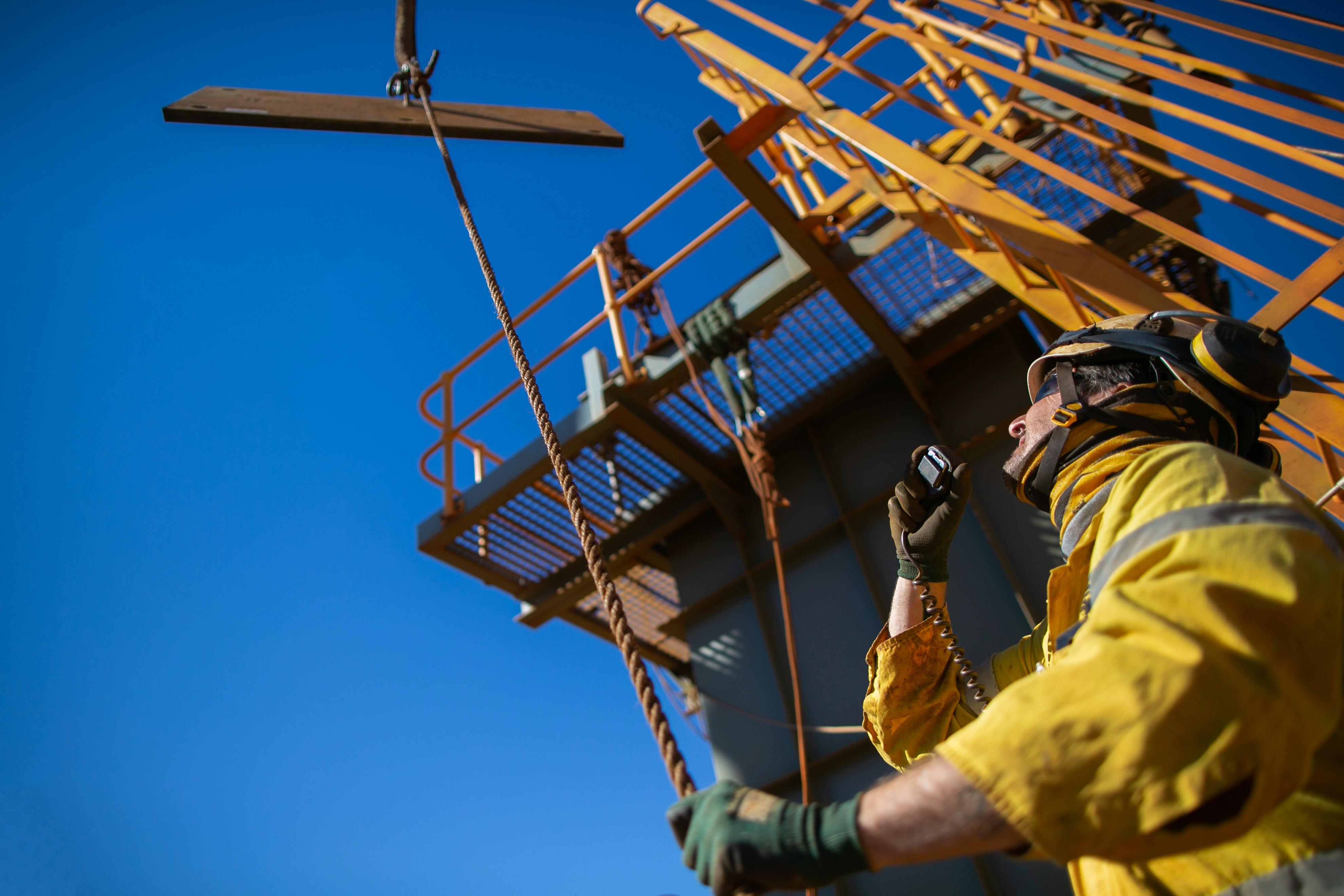
14/09/2020
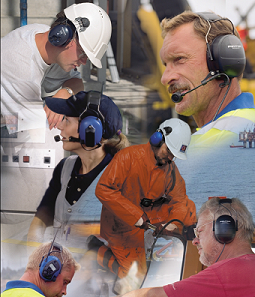
15/06/2020
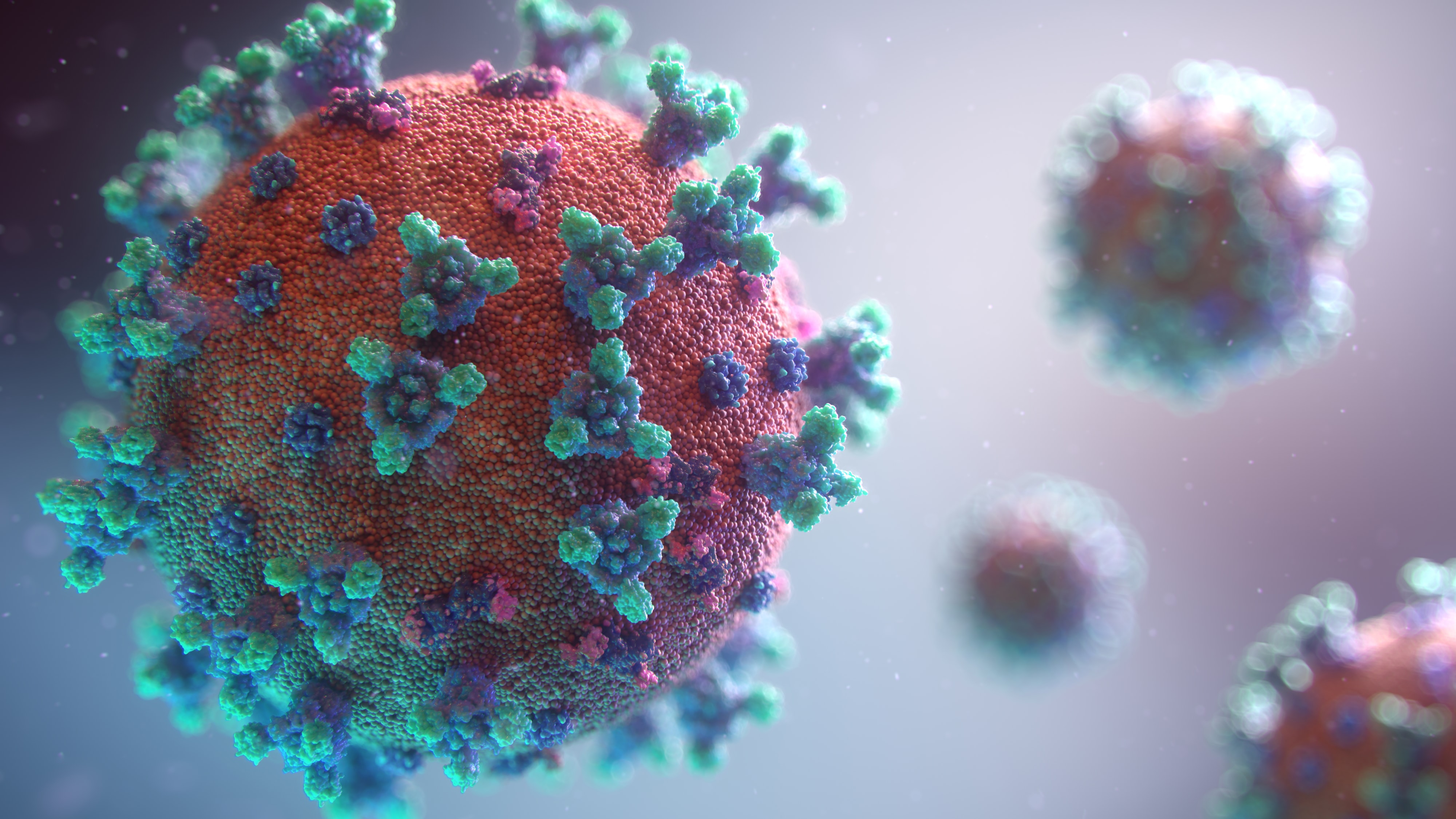
22/05/2020
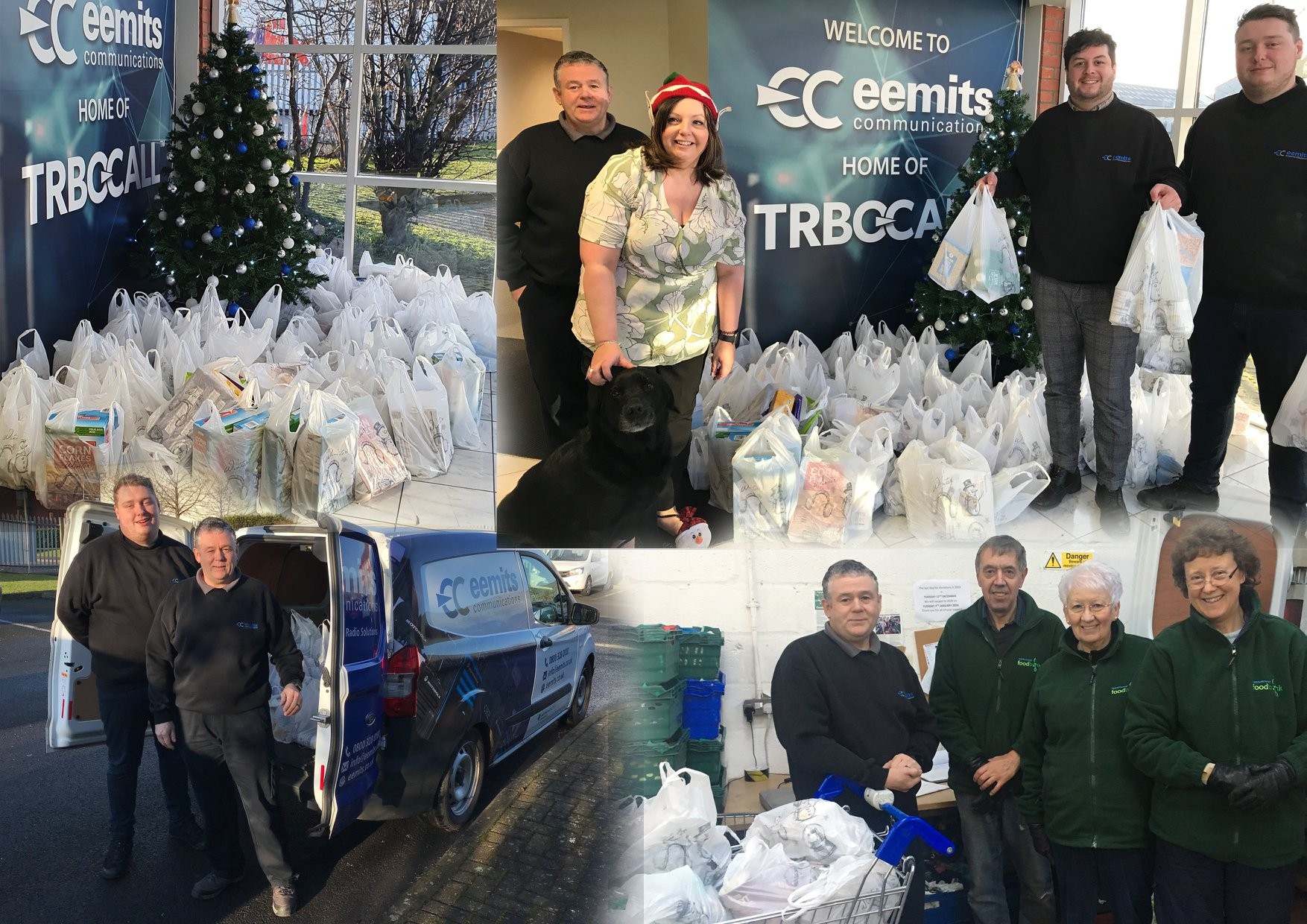
18/12/2019
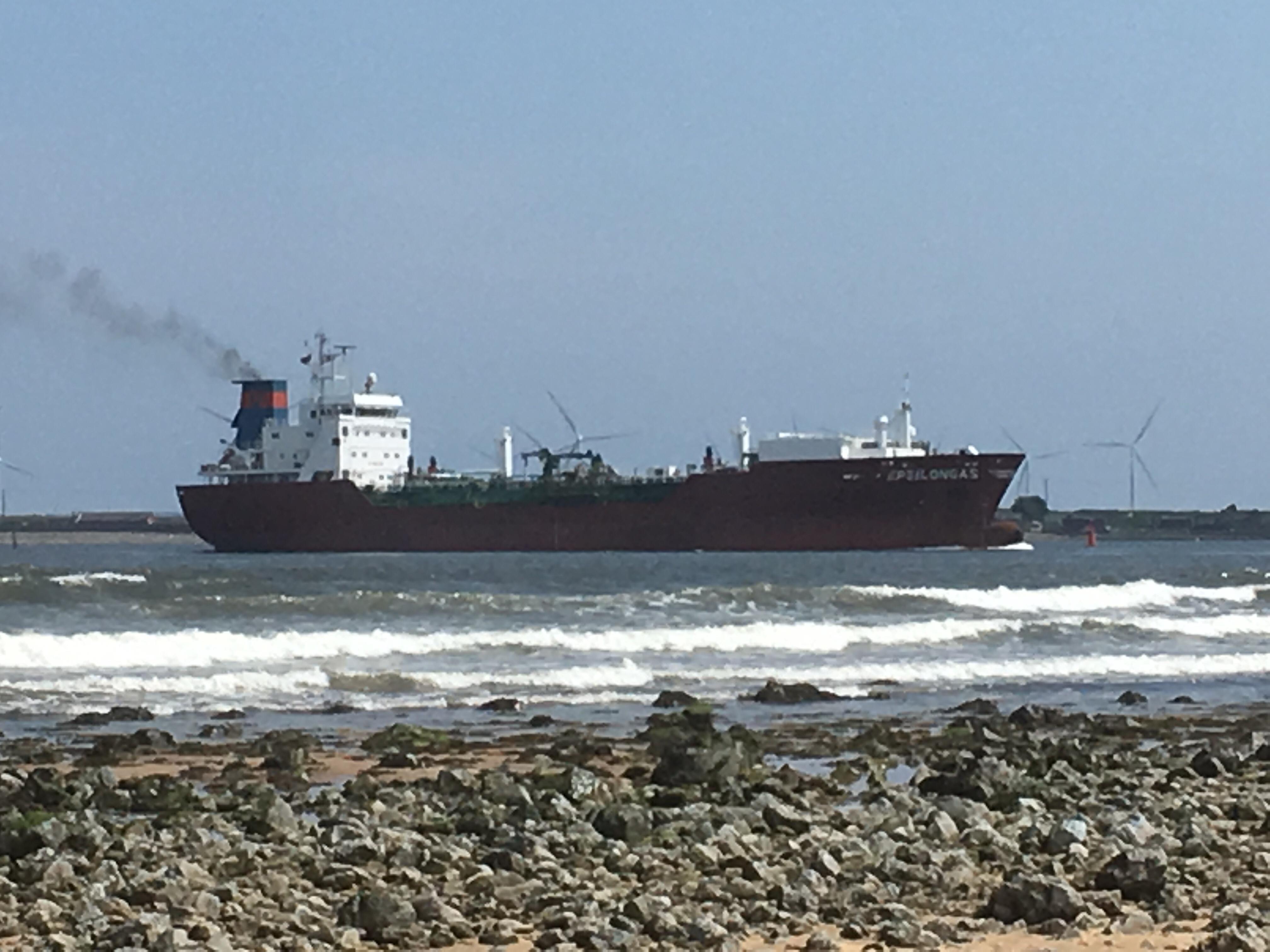
31/07/2018
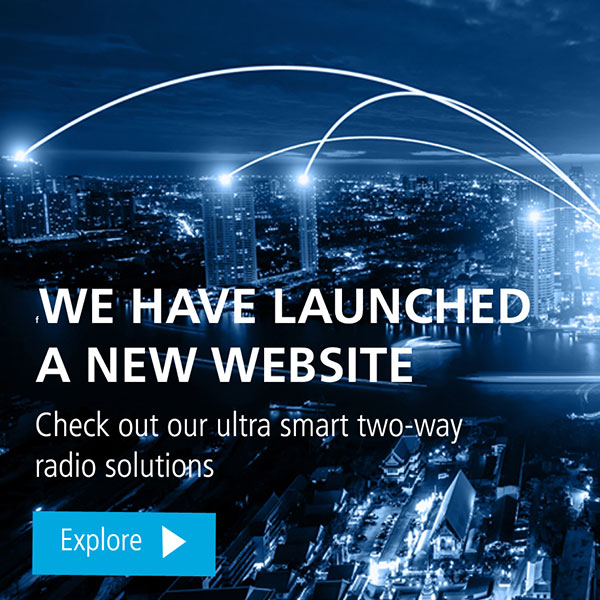
20/02/2018
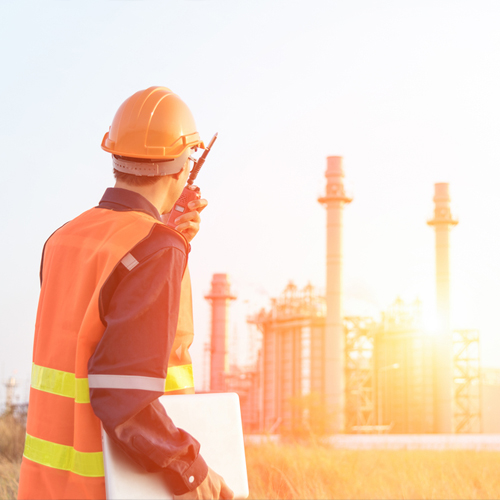
05/10/2017
See What Our Clients Say
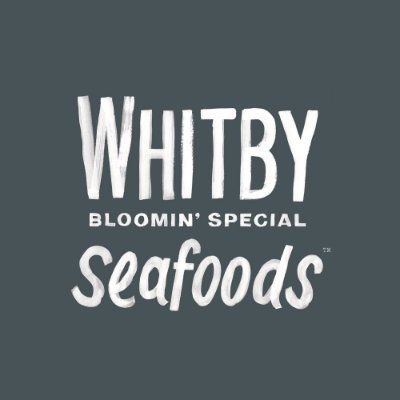
“Eemits Communications has been a long-time partner of Whitby Seafoods. Their single-site conventional digital repeater system has driven daily efficiency and given us greater on-site access control. We appreciate their continued commitment to customer satisfaction and look forward to what the future holds.”
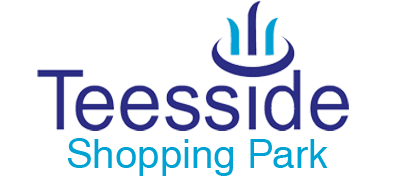
"We have a great and longstanding working relationship with Eemits and they have always ticked every box. They offer an excellent, friendly and reliable service.
Eemits have a great understanding of the park and its needs for the customer and our retailers. With a positive can-do attitude, they never say no."
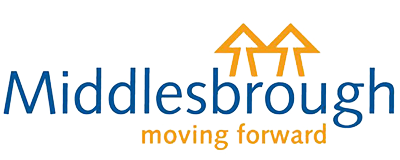
"We started working with Eemits following on from a recommendation from another customer. They provided us with a solution that suits our needs and they continue to supply the best service with no issues.
Eemits is a professional, friendly and reliable company."
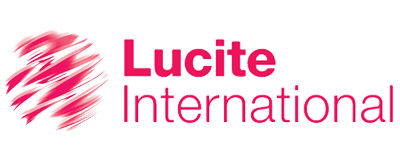
"Eemits continue to provide us with a great supportive service consistently being very helpful. The whole team is great and it's very clear the staff have a great knowledge of the products and are happy to pass this on.
Eemits is a great company."
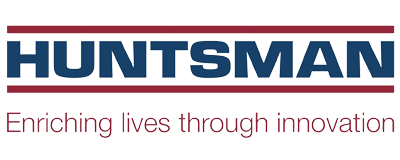
"The service offered by Eemits is second to none, we have a great working relationship with them and the contract we have is good value for money."
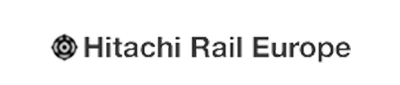
"We needed two-way radios for the guys on the test track and something that was scalable. The solution Eemits provided was far superior in comparison to other competitors offerings.
Everything is done in-house and the service and sales department is particularly good. As masters in their field they are extremely knowledgeable."
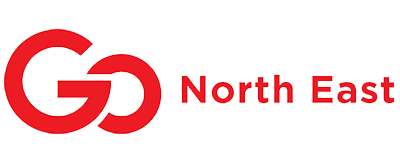
"Eemits dedicate a lot of time to us as a customer - we feel like we get a personal touch. They're excellent and go above and beyond. They'll put the work in - i.e. training users.
Good quality, good people, good team, all of who are positive about their company. They demonstrate real passion."
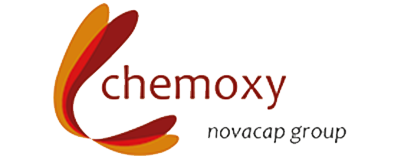
"The quality of service that Eemits provides is excellent. The team is very knowledgeable and they offer high quality products. The TRBOCALL solution fitted meets our site requirements and upgrades our technology.
Lone worker function is particularly useful allowing us to monitor our staff ensuring they are safe at all times."

"Eemits Communication is friendly, professional and competitive. They are excellent and their workmanship and knowledge is great.
Eemits attitude sets them apart - no problem is too big"
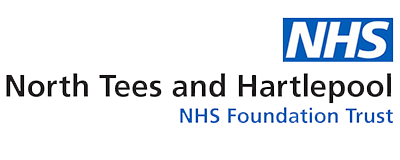
"Prior to the installation of our current system onsite communications were poor. Eemits Communications offered us guidance and advice on the different technologies available and delivered a highly effective system on time and within our budget. Its success has led to other departments using the system."
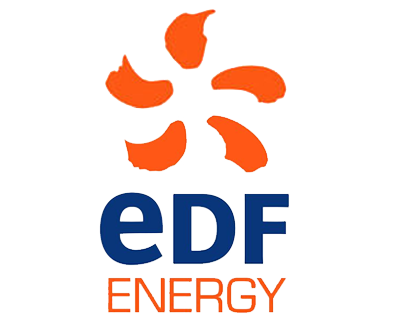
"Eemits Communications Ltd have been involved in work at Hartlepool Power Station for over 10 years now. During this time they have installed an Aerial network through our buildings to enable more efficient internal radio communications.
I have found the staff highly professional at all times and willing to provide help whenever they can, I would have no hesitation in recommending this company."
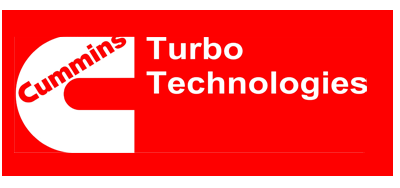
"Having previously worked with Eemits, we knew that we were dealing with a supplier that we could trust and one that could help us to significantly increase the safety of our lone workers with its unique solutions.
The equipment supplied by Eemits is excellent. We have been greatly impressed by the knowledge and skills of their engineers who have carried out the onsite surveys and installation of the system.
Eemits came up with an innovative approach to overcome challenges that we had with installing a system with the structure of our building, and as such, the quality of radio frequency is outstanding."
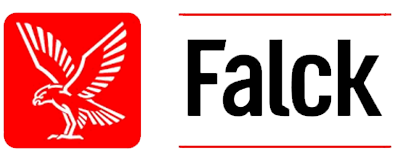
"The service delivered by Eemits has been excellent and we have developed a very good working relationship over the years.
As a local business to Falck Fire Services they can respond to faults or general requests very quickly - which is very important in our line of work - whereas similar suppliers have a greater response time.
TRBOCALL is an overall platform that has made a massive improvement to our communications in comparison to the analogue system that we had been using for many years. It provides us with many different applications that can be utilised across the business.
Since introducing TRBOCALL we have seen significant improvements related to safety and in our communications itself, which is critical to our operations."